Table Of Contents
Enhance your B.Tech path with quantum notes from Aktu that include important and commonly repeated questions on advanced welding. Dive into this resource for in-depth learning and exam success. Unit-4 Repair and Maintenance Welding
Dudes 🤔.. You want more useful details regarding this subject. Please keep in mind this as well. Important Questions For Advance Welding: *Quantum *B.tech-Syllabus *Circulars *B.tech AKTU RESULT * Btech 3rd Year * Aktu Solved Question Paper
Q1. What is hardfacing principle of operation of hardfacing ? Mention advantages and applications of hardfacing.
Ans. A. Hardfacing:
- 1. In hardfacing, metal is placed over another surface to increase its hardness and make it resistant to abrasion, convolution, impact, erosion, and other wear-and-tear processes.
- 2. Abrasion resistance is one of hardfacing’s most crucial applications.
- 3. Since the efficiency of the hardfacing diminishes excessive dilution, three layers of hardfacing alloys are coated on general purpose surfaces.
B. Objectives of Hardfacing:
- 1. By depositing metals or alloys that will provide them resistance to wear or abrasion, corrosion, heat, impact, erosion, cavitation, hammering, and indentation, on these components and assemblies, it is possible to increase their service life.
- 2. To rebuild a worn or scratching out incorrectly cast part.
- 3. To repair a component.
C. Principle of Operation of Hardfacing:
- 1. The success and quality of the surfacing procedure depends on knowing the precise composition of the base metal.
- 2. Determine the type and degree of wear of the base metal.
- 3. Determine the welding position of the job.
- 4. Estimate the area that needs to be hardfaced.
- 5. Select an appropriate hardfacing alloy.
- 6. Select an appropriate hardfacing method.
- 7. Prepare the surface to be hardfaced.
- 8. Apply the hardfacing alloy on the base metal.
- 9. Impart proper surface finish to the hardfaced base metal component.
D. Advantages:
- 1. This lengthens the product’s useful life.
- 2. The corrosion resistance is imparted by this.
- 3. This procedure is less expensive than other processes.
- 4. A lower level of worker is needed.
E. Applications of Hardfacing:
- 1. This is widely utilized in construction equipment, including engine valve facing, scraper and bulldozer blades, and textile industry equipment.
Q2. Explain in detail the advantage of hardfacing with oxyacetylene torch.
Ans.
- 1. With the help of portable and inexpensive equipment, the oxy-acetylene welding procedure can be employed for surfacing.
- 2. In this surfacing process, the parent metal is heated and cooled at very slow rates, which causes very little dilution and produces surfacing deposits that are smooth, exact, and of exceptionally high quality.
- 3. Grooves, small gaps, and recesses may be filled with ease, and extremely thin layers can be applied smoothly.
- 4. Oxy-acetylene surfacing techniques’ delayed cooling and preheating characteristics tend to reduce cracking even in materials that are extremely wear resistant but brittle when exposed to certain welding flame types and tip sizes.
- 5. No flux is required during surface; instead, a low melting point, high carbon filler metal is often deposited.
- 6. This procedure can also be performed using powdered material; in this case, a welding torch with a hopper is used (a powder feeding device).
- 7. Where many identical pieces that may be arranged in a systematic way are present, the oxy-acetylene surfacing procedure can be carried out semi-automatically.
- 8. The procedure is simple to use in the field, and hardfacing alloy can be put in extremely thin layers.
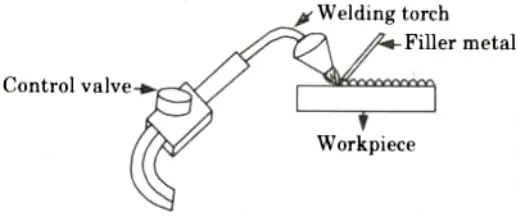
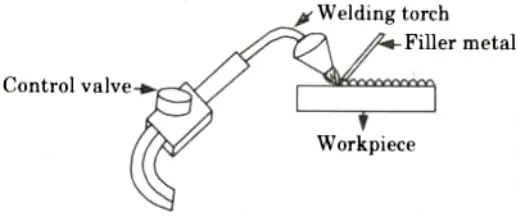
Q3. Explain the effect of various alloying elements on weldability.
Ans.
- 1. Alloying elements increase or decrease hardenability of the HAZ. C, Mn, Mo, Cr, V, Ni and Si have greatest effect on the hardenability of steel.
- 2. Alloying elements provide grain refinement. Al, V, Ti, Zr and N are the grain refiners for carbon and low alloy steels.
- 3. Alloying components regulate the temperature at which ductile materials become brittle.
- 4. By strengthening the metal through solid solution hardening, alloying elements create substitutional alloys.
- 5. In order to boost mechanical characteristics via lattice distortion, alloying elements create interstitial alloys.
- 6. Alloying elements diminish segregation, generate carbides, and age-hardening precipitates.
- 7. Alloying components also refine grain.
- 8. Alloying elements provide deoxidation of molten metal without loss of primary alloying elements. Ti, Zr, Al, Si have affinity for oxygen than iron and thus act as deoxidizers in carbon and low alloy steels.
Q4. What are the welding characteristics of aluminum and its alloys ? Mention various methods for welding aluminum and its alloys.
Ans. A. Welding Characteristics of Aluminium and its Alloys:
- 1. The impact of the thin coating of oxide that is chemically or physically removed before welding is the first and most important factor to take into account.
- 2. Because aluminium is such a superb heat conductor, heat from the welding joint is dissipated very quickly. The use of larger nozzle sizes must be used to make up for this.
- 3. The linear expansion coefficient of aluminium is high.
- 4. When welding thinner sections that could buckle, greater caution is needed since aluminium becomes weak when heated.
- 5. Aluminum does not change colour when heated, and it may be challenging to determine when the metal starts to melt without experience.
B. Various Methods for Welding Aluminium and its Alloys:
- 1. Oxy-gas welding.
- 2. MIG or TIG welding,
- 3. Resistance welding,
- 4. Metallic arc welding,
- 5. Solid state welding, and
- 6. Atomic-hydrogen welding.
Q5. Explain in detail aluminum welding by double operator method.
Ans.
- 1. Using a double operator welding technique, as shown in Fig.
- 2. The melting point of the aluminium oxide (alumina Al2O3), which is constantly present as a surface coating and is created when metal is heated, is substantially higher than that of aluminium.
- 3. It would spread throughout the weld if it were not removed, making it weak and brittle.
- 4. Sheets under 20 gauge can be turned up at a right angle and welded without the use of a filler rod after the work is cleansed of grease and brushed with a wire brush.
- 5. Because aluminium is so fragile while it is close to melting, it is important to ensure that the welding process doesn’t cause any collapsing.
- 6. The flame is adjusted to have just a tiny bit too much acetylene, neutralised, and a rod of pure aluminium or an alloy with 5% silicon should be somewhat thicker than the portion to be welded.
- 7. For sheets thicker than 6 mm, the double operator method is utilised; the blow pipes and rods are angled at 50–60° and 70–80°, respectively.
- 8. This method gives a great increase in welding speed.
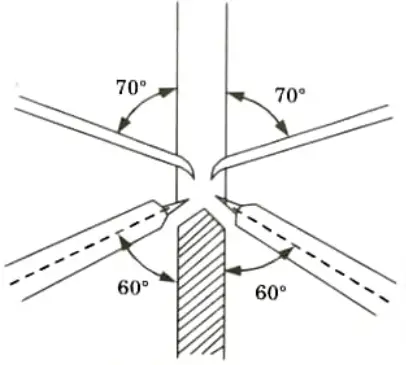
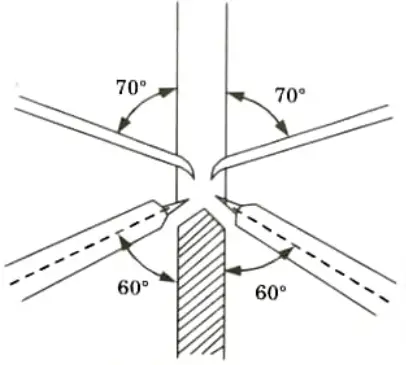
Q6. Discuss the various techniques for welding the dissimilar materials.
Ans. Various techniques for welding the dissimilar materials are as follows:
- i. Resistance Welding:
- 1. Resistance welding procedures frequently reduce the risk of the production of brittle intermetallic compounds within the joint, making it easier to create suitable junctions between dissimilar metals than arc welding because no fluxing or inert atmosphere provision issues are present.
- 2. For instance, when copper and aluminium are fused together, they generate a number of brittle phases, but flash-butt welding of the two metals is commonly used because these phases are pushed out of the joint when the upset force is applied.
- 3. Dissimilar metals are welded using both spot welding and projection welding.
- ii. Solid-State Welding:
- 1. Solid-state welding processes include:
- i. Pressure welding with or without controlled atmospheres.
- ii. Ultrasonic welding.
- iii. Friction welding.
- iv. Diffusion bonding.
- 2. It is necessary that the surfaces should be clean and be in intimate contact.
- 1. Solid-state welding processes include:
- iii. Brazing :
- 1. Brazing is crucial for bonding dissimilar metals because it prevents alloying between the metals and the formation of inappropriate phases when done properly.
- 2. Normally, annealing should be done on materials that are prone to intergranular penetration before brazing.
- 3. Copper, copper alloys, steels of all types, heat-resistant alloys, and nickel alloys can be joined using zinc carrying silver solders and copper-zinc alloys.
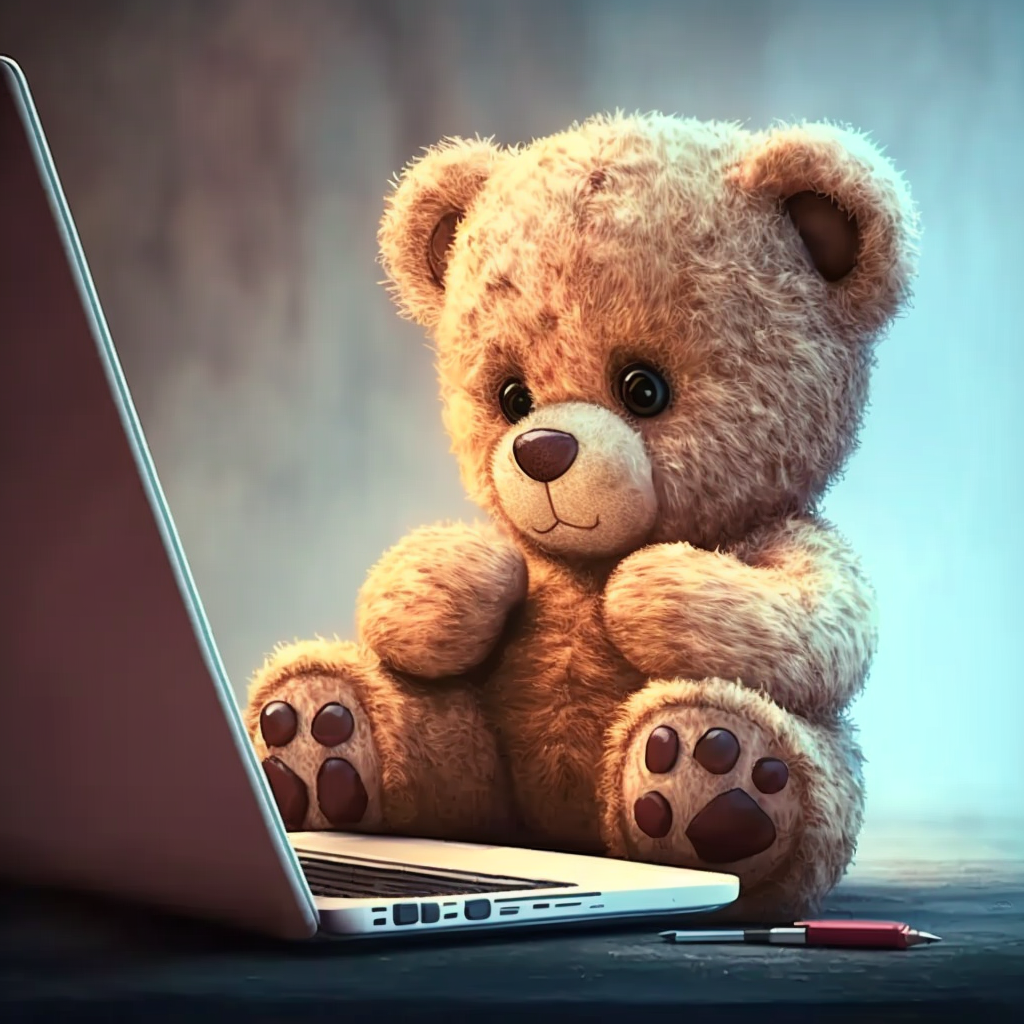
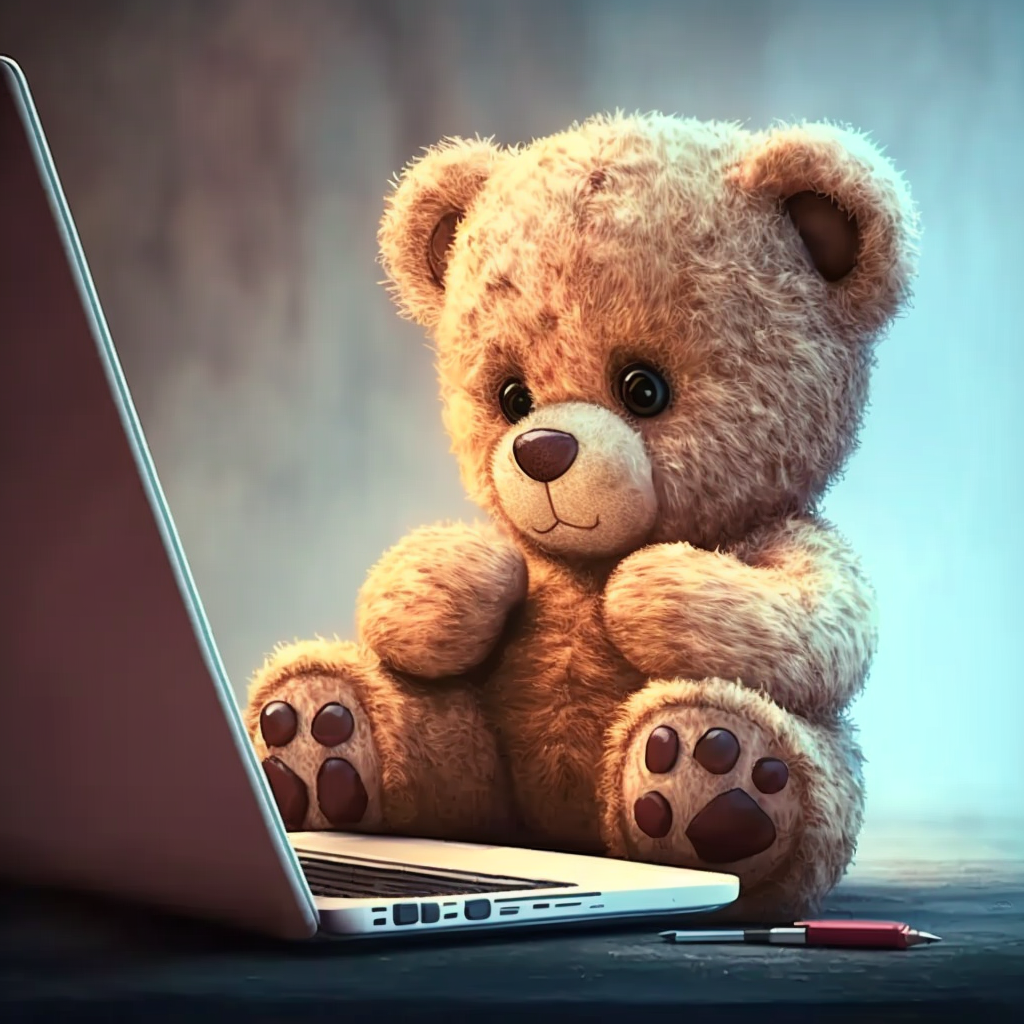
Important Question with solutions | AKTU Quantums | Syllabus | Short Questions
Advance Welding Btech Quantum PDF, Syllabus, Important Questions
Label | Link |
---|---|
Subject Syllabus | Syllabus |
Short Questions | Short-question |
Question paper – 2021-22 | 2021-22 |
Advance Welding Quantum PDF | AKTU Quantum PDF:
Quantum Series | Links |
Quantum -2022-23 | 2022-23 |
AKTU Important Links | Btech Syllabus
Link Name | Links |
---|---|
Btech AKTU Circulars | Links |
Btech AKTU Syllabus | Links |
Btech AKTU Student Dashboard | Student Dashboard |
AKTU RESULT (One View) | Student Result |