Use our AKTU question paper and solution to learn Quantity Estimation and Construction Management. Learn how to accurately estimate project requirements and manage construction operations efficiently. Increase your knowledge of the subject.
Dudes 🤔.. You want more useful details regarding this subject. Please keep in mind this as well. Important Questions For Quantity Estimation and Construction Management: *Quantum *B.tech-Syllabus *Circulars *B.tech AKTU RESULT * Btech 3rd Year
Section A: Quantity Estimation and Construction Management Short Questions
a. Define Estimation.
Ans. Estimation is a technique that helps us figure out how much it will cost, how many tools and workers we’ll need, and how long it will take to finish the job.
b. Differentiate between revised and supplementary estimation.
Ans. A Supplementary Estimate: While a work is in progress, some revisions or more work may be considered required for the development of a project owing to material departure of a structural character from the design originally approved. After that, an estimate is prepared that includes all such work. This is referred to as a supplementary estimate.
Revised Estimate: A revised estimate is a comprehensive estimate for the revised quantities and rates of items of work originally supplied in the estimate that do not have major structural deviations from the design authorized for the project.
c. How you can calculate the earliest expected time and latest allowable occurrence time in PERT?
Ans. Earliest Expected Time (TE): It is the time when an event can be expected to occur earliest. TE calculated as : (TE) = (TE)i + ti-j.
Latest Allowable Occurrence Time (TL): The latest time by which an event must occur to keep the project on schedule is called the latest allowable occurrence time (TL). TL is determine as :
(TL) = (TL)j + ti-j
d. Differentiate between event and activity.
Ans.
S. No. | Event | Activity |
1. | Event is a point when certain conditions have been fulfilled, such as the start or completion of one or more activities. | Activities take place between events. |
2. | An event consumes neither time nor any other resource. | Activity is an item of work involving consumption of a finite quantity of resources and it produces quantities results. |
e. Define optimistic time and pessimistic time used in PERT.
Ans. Optimistic Time: It, expressed as ‘to’, represents estimate of minimum possible time by which an activity can be completed assuming that everything is in order according to the plan and there can be only minimum amount of difficulty.
Pessimistic Time: It expressed as ‘tp’ represents estimate of maximum possible time by which an activity can be completed assuming that things may not be in accordance with the plan and there can be incidence of difficulties in carrying out the activity.
f. Enlist the factors affecting the selection of equipments.
Ans. Following are the factors affecting the selection of equipments:
- i. Easting equipment.
- ii. Operating cost.
- iii. Availability of equipment.
- iv. Economic life.
- v. Study of site condition.
- vi. Suitability of equipment for future.
- vii. Size of equipment.
g. Write down the advantages of hoisting equipments.
Ans. Following are the advantages of hoisting equipments:
- i. It can lift the load and place it on the desired location.
- ii. The load can be hold in suspension during transfer from one location to other.
h. What do you mean by cash flow diagram ?
Ans. A cash flow diagram is a graphical representation of cash flows, including both cash outflows and cash inflows, with relation to a time scale.
i. Define interest rate. How interest rate can be classified.
Ans. Interest Rate: It is the cost of borrowing debt capital, often known as the cost of money. To put it another way, interest rates convert money today into money tomorrow; it is the rate at which money increases when invested.
Classification:
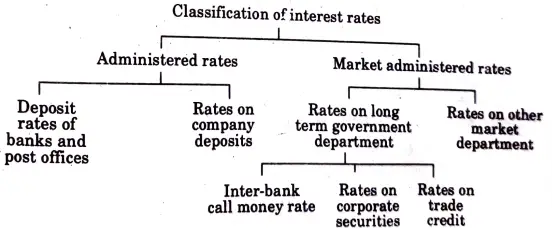
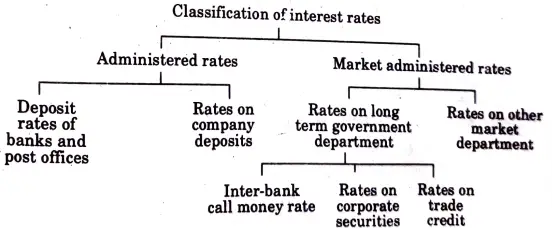
Section B: Aktu Questions with Long Answers
a. Classify the various types of estimation that are used in estimation of building.
Ans. Estimates can be grouped into two main categories:
A. Approximate Estimates: An approximate estimate is a rough estimate created to obtain an approximate cost in a short period of time.
B. Detailed Estimates:
- 1. A detailed estimate of a project’s cost is generated by establishing the quantities and pricing of everything that a contractor is required to deliver and execute in order for the work to be completed satisfactorily.
- 2. It is the most accurate and dependable type of estimate.
- 3. A detailed estimate may be prepared in the following two ways:
- i. Unit-quantity Method:
- a. The unit-quantity method divides the job into as many processes or items as are required.
- b. A measuring unit is chosen.
- c.The total amount of work under each item is calculated in the appropriate unit of measurement.
- d. The total cost per unit quantity of each item is calculated.
- e. The total cost of the item is then calculated by multiplying the cost per unit quantity by the number of units.
- f. The advantage of this method is that the unit costs on different works can be simply compared, and the total estimate can be quickly rectified for variations in quantities.
- ii. Total-quantity Method: In this method, an item of work is divided into the following five subdivisions:
- a. Materials,
- b. Labour,
- c. Plant,
- d. Overheads, and
- e. Profit.
The total quantity of each type or class of material or labour is determined and multiplied by its individual unit cost. Similarly, the plant cost, overhead expenses, and profit are calculated.
b. List the information which should customarily appear in an advertisement for tenders.
Ans.
- 1. For contract employment, especially in an open bidding system, the jobs must be properly advertised. A formal notice inviting tender (NIT) is commonly published in major national and local newspapers.
- 2. The NIT is also posted on notice boards in departments soliciting bids. Nowadays, the internet is also used.
- 3. NIT is uploaded on company’s official website or the concerned government department with the following details:
- i. Name of the authority inviting the bids,
- ii. Name of the project,
- iii. Conditions for eligibility of contracting àgencies to submit a bid,
- iv. Brief details of the project,
- v. Estimated cost and time of completion of the project,
- vi. The cost of the tender documents,
- vii. Earnest money to be deposited with the completed tender,
- viii. Date and time by which the bids are to be submitted and the place of submission,
- ix. The date and time of opening of the bids, and
- x. Validity of the tender, etc.
- 4. In addition to the information and conditions mentioned in the typical tender notice, the tender notice includes the following: refund of earnest money, period of validity of rates quoted, site inspection, not relative of contractor, rates to include all taxes (about 2% of gross amount), source and specification of materials, change of address, and so on.
- 5. When the tender form is collected from the office, all such details will be included in the tender notice. These items are not mentioned in the contract. As a result, the tender notice is a critical document upon which subsequent agreements with contractors are founded.
- 6. Therefore, it is necessary that the tender notice must be included in the contract document.
c. Draw a bar chart and compute the total duration of the project from the data given below :
Task 1 | 5 days |
Task 2 | 3 days |
Task 3 | 7 days |
Task 4 | 2 days |
Task 5 | 4 days |
Task 1 and 4 will be started together. Task 2 will start, after completion of task 3 and task 3 will take place after task 1. Task 5 will be taken only after completion of task 3.
Ans. Given: Task table.
To Find: Draw bar chart and total duration of project.
1. Bar Chart:
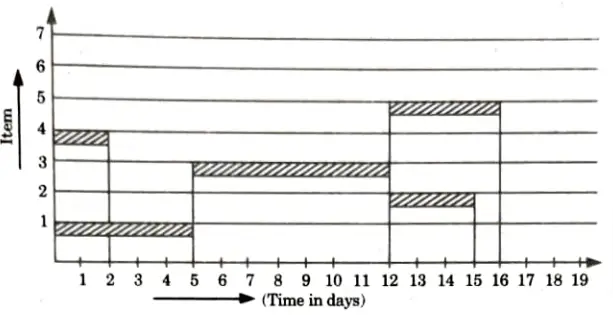
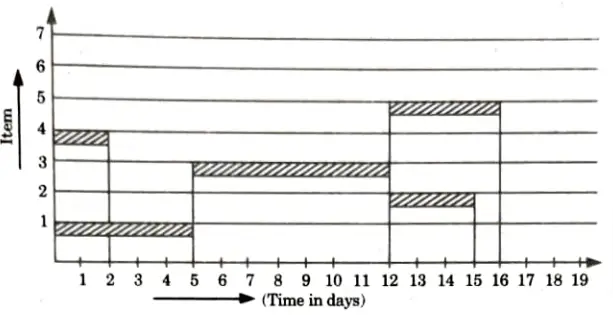
2. Total duration of the project = 5 + 7 + 4 = 16 days.
d. Categorize about various types of earth work equipments with special purpose usage for each equipment.
Ans. Excavating and Earth Moving Equipment: Following are the excavating and earth moving equipment:
- 1. Power Shovel:
- i. Basic parts of power shovel including the track system, cabin, cables, rack, stick, boom foot-pin, saddle block, boom, boom point sheaves and bucket.
- ii. Bucket size varies from 0.375 m3 to 5 m3.
- iii. Uses:
- a. Suitable for close range of work.
- b. Capable of digging very hard materials.
- c. Can remove big sized boulders.
- d. To excavate the earth and to load the trucks.
- e. It is used in various types of jobs such as digging in gravel banks, clay pits, digging cuts in road works, road-side berms, etc.
- 2. Back Hoe:
- i. It is also known as hoe, back shovel and pull shovel.
- ii. The basic parts are boom, jack boom, boom foot drum, boom sheave, stick sheave, stick, bucket and bucket sheave.
- iv. Uses:
- a. It is the best machine for digging beneath the machine level, such as trenches, footings, and basements.
- b. It can be used efficiently to dress or trim the surface, eliminating the need for manual effort to dress the excavated surface.
- 3. Drag Line:
- i. The drag line gets its name from the visible activity of dragging the bucket against the material to be excavated.
- ii. Unlike the shovel, it features a long light crane boom to which the bucket is loosely linked through wires.
- iii. Because of its design, a dragline can dig and dump over greater distances than a shovel.
- iv. Drag lines can be used to delve below the track level and handle softer materials.
- v. The drag line’s basic components, which include the boom, hoist cable, drag cable, hoist chain, drag chain, and bucket.
- vi. Uses:
- a. It is the best machine for dragging softer material and stuff that is below its track level.
- b. When the sides are given the freedom to determine their angle of repose without shoring, it is particularly helpful for trench excavation.
- c. It is mostly employed in the excavation of canals and the placement of material on embankments without the need of hauling units.
- 4. Clam Shell:
- i. This is so named because of how much its bucket resembles a clam, a shellfish with a hinged double shell.
- ii. The front end resembles a crane boom in essence, with a specifically made bucket loosely fastened at the end through wires like a drag line.
- iii. A clam shell bucket’s capacity is often expressed in cubic metres.
- iv. The closure line, hoist line, sheaves, brackets, tagline, shell, and hinge are the main components of a clam shell bucket.
- v. Uses:
- a. Used for handling loose material such as crushed stone, sand, gravel, coal etc.
- b. Main feature is vertical lifting of material from one location to another.
- c. Mainly used for removing material from coffer dam, sewer main holes, well foundations etc.
- 5. Trenching Machine:
- i. Trenchers are tools used to dig trenches or ditches with a range of widths and depths.
- ii. There are two different types of trenching equipment: wheel type and ladder type.
- iii. Operation is quick when the necessary depth or width is provided.
- iv. Used to dig trenches for installing pipelines, sewer lines, cables, etc.
- 6. Scrapers:
- i. Unique machine for digging and long-distance hauling of plough able materials.
- ii. The basic parts of scrapers are the bowl, apron and tail gate or ejector.
- iii. It is a self-operating machine.
- iv. Wheels of machine cause some compaction.
- 7. Bulldozer:
- i. The heavy blade attached to the tractor pushes the material from one place to another.
- ii. The tractor can be of the crawler or the wheeled type.
- iii. Uses:
- a. For spreading the earth fill.
- b. For opening up pilot roads through mountainous and rocky terrains.
- c. Clearing land from the trees and stumps.
- d. Back-filling trenches at construction sites by dragging the earth from one place to another.
e. What is cost planning ? Discuss the different types of cost used in cost planning with their relative graph.
Ans. A. Cost Planning:
- 1. The estimate to fulfill each of these can be created based on the unit cost of the resources and the overall amount of resources needed once the resource need has been determined. Cost planning is the name of the procedure, which is essential for managing project costs.
- 2. The essential components of a cost plan are the project schedule and estimates.
B. Types of Cost:
- 1. Direct Cost:
- i. It is financially possible to allocate direct costs directly to the object.
- ii. In the construction industry, direct costs include any costs for labour, materials, equipment, etc. that are directly related to the cost object.
- 2. Indirect Cost:
- i. Indirect costs are those that cannot be traced back to a specific cost object.
- ii. It should not be feasible from a financial standpoint.
- iii. On some basis, indirect costs are often assigned to a cost object.
- iv. In the construction industry, any expenditures necessary for installation completion but not directly linked to the cost object are considered indirect costs, such as overhead.
- v. Indirect expenses in manufacturing are those that cannot be tied directly to the finished good or production method.
Section 3: Work Calculated in Estimation of Buildings
a. In Figure below, the.plan represents the plan of superstructure wall of a single room building of 5 m x 4 m, and sections represent the cross-sections of the walls with foundation. Estimate the quantities of:
i. Earthwork in excavation in foundation.
ii. Concrete in foundation.
iii. Brickwork in foundation and plinth.
iv. Brick work in superstructure.
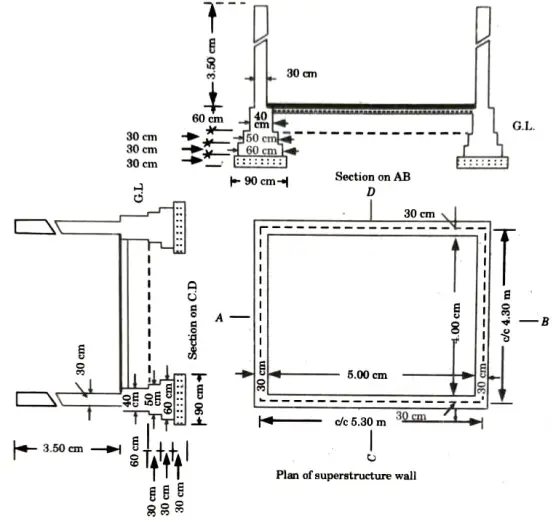
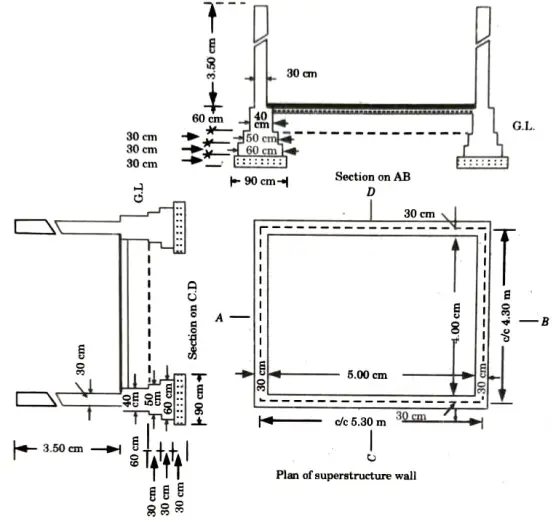
Ans. Given: Fig.
To Find: 1. Earthwork in excavation in foundation.
2. Concrete in foundation.
3. Brickwork in foundation and plinth.
4. Brickwork in superstructure.
1. The length of long wall centre to centre = 5.00 + (1/2) x 0.30 + (1/2) x 0.30 = 5.30 m.
2. The length of short wall centre to centre 4.00 + (1/2) x 0.30 + (1/2) x 0.30 = 4.30 m.
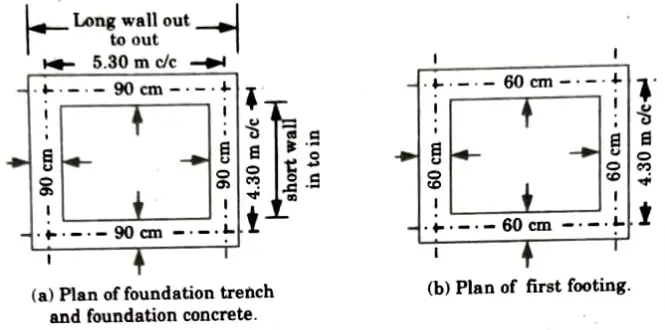
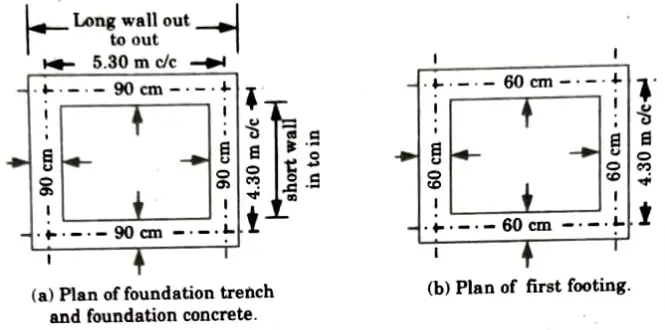
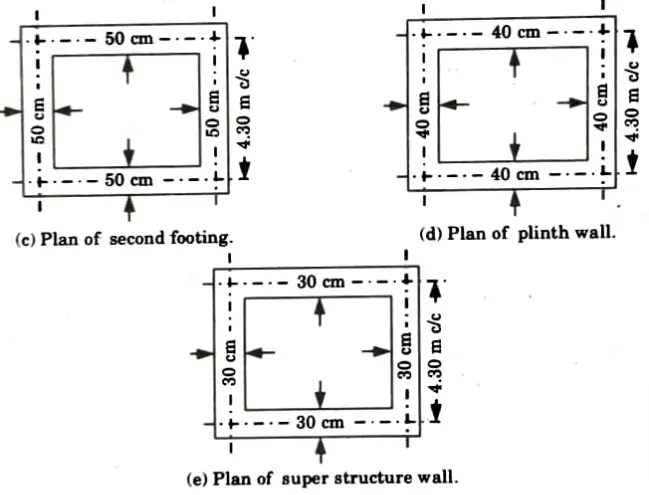
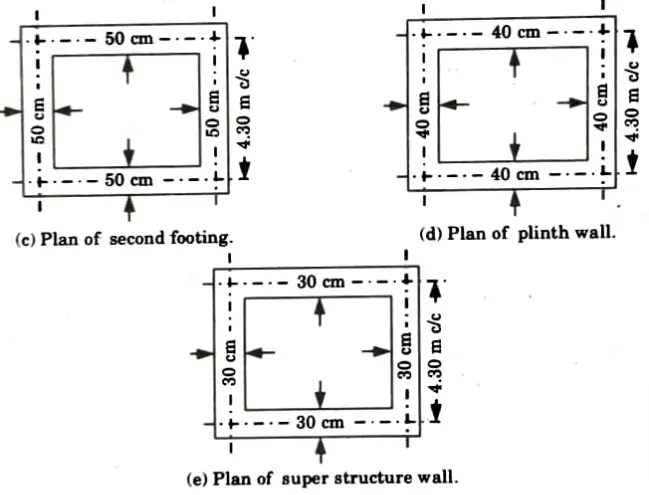
3. The plans for the foundation trench, foundation concrete, and each footing or set of stairs for the wall are presented in Fig. to help with quantity estimation.
4. Then the long wall in-to-in and the short wall in-to-in of each part may be dealt one by one.
5. Details of measurement and calculation of quantities:
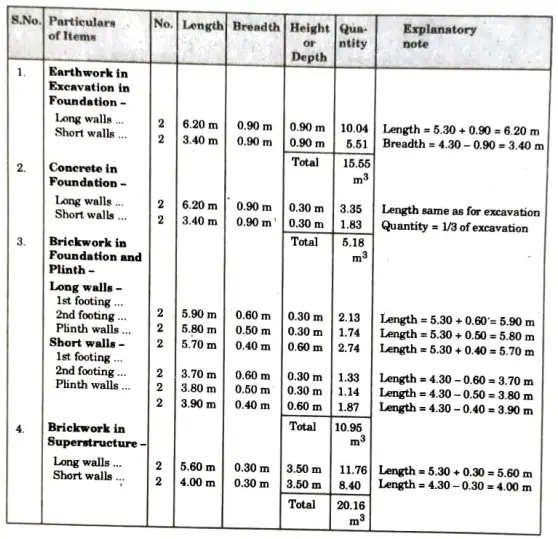
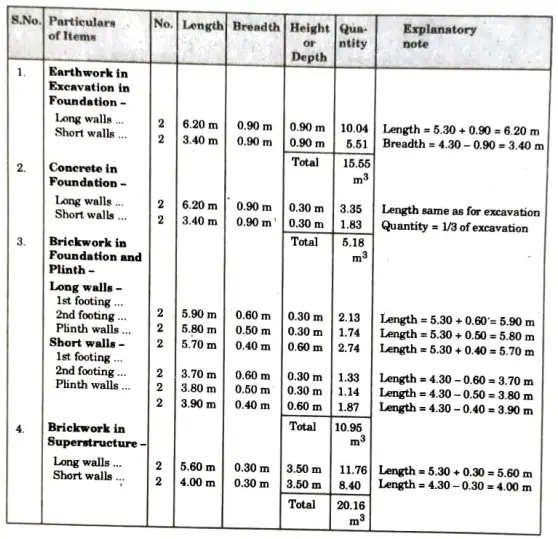
b. Categorize the main items of work calculated in estimation of buildings.
Ans. Main Items of Work: Following are the main items of works and their measure units:
- 1. Earthwork
- 2. Concrete in Foundation
- 3. Soiling
- 4. Damp Proof Course (DPC)
- 5. Masonry
1. Lintels over Openings:
- i. Lintels are constructed in RCC and estimated in m.
- ii. Length of the lintel is equivalent to the two bearings width plus clear span.
- iii. It is considered as the thickness of lintel with a minimum of 12 cm.
- iv. If the dimension of bearing is not provided. The length of lintel is given by L = s + 2t, s = clear span, t = bearing width.
- v. Quantity of lintel = L x thickness of the wall x t.
2. RCC Work:
- i. RCC activity may be in the beams, roof, lintels, foundation, floor slab, columns etc and the quantities are determined in m.
- ii. Centering and shuttering quantities in building estimation are calculated in m².
- iii. Including bending the reinforcement is measured in MT (metric tons). In general, 0.6 % to 1% of RCC by volume are taken for steel calculation.
3. Flooring and Roofing :
i. Ground Floor:
The base PCC (plain cement concrete) and floor finishing of CC (cement concrete) or marble or vitrified tiles etc are taken as one job and quantity are calculated in m2 (length x breadth).
ii. 1st floor, 2nd floor etc:
- a. Supporting structure for 1st floor and 2nd floor is cast in RCC and quantity is measured in m3.
- b. Floor finishing is laid in marble CC or vitrified tiles etc and quantities in building estimation are measured in m².
iii. Roof:
- a. Supporting structure is cast in RCC and quantities are calculated separately in building estimation in m3.
- b. Terrace water proofing and protection screed of 75 mm to 120 mm thick is calculated in m² under the separate item.
- c. In case of galvanized iron sheet or tile or asbestos cement sheet roofing, the roof covering is determined including overlays with all fitting in m2.
- d. Supporting trusses and members are taken as a separate item in kgs.
4. Plastering:
- i. 12 mm thick plastering is normally used in general for a brick wall and it is measured in building estimation in m2.
- ii. Both sides of the walls are granted as solid and estimations are exercised for both sides.
5. Doors and Windows:
i. Frames or Chowkhat:
Window and Door frame estimation is done in m2.
ii. Doors and Window Shutters:
They are calculated in m² by multiplying the breadth by the height of the shutters.
6. Woodwork: Wooden roof trusses. Wooden beams, frames, posts, interior items like TV units, wardrobes, modular beds, kitchen, etc., comes under this woodwork and quantities are estimated in m3.
7. Ironwork:
- i. Ironwork is measured in kgs or MT by multiplying the weights per running meter (Unit weight).
- ii. Iron holdfasts weight may be considered as 1.5 kg each. For doors, 6 holdfasts and for windows 4 holdfasts are considered.
- iii. The weight of nuts, bolts and rivets with heads is estimated by counting their sizes, numbers and using steel tables.
- iv. For steel roof truss 5 % of the steelwork is provided for rivets, bolts and nuts.
8. Whitewashing or Colour Washing:
- i. Whitewashing or colour washing quantities are measured in building estimation in m² and these quantities will be the same as the quantities of plastering.
- ii. Two coats of paint are considered for whitewashing or colour washing.
9. Doors and Window Painting:
- i. Painting or varnishing of doors and windows are calculated in building estimation in m².
- ii. The following multiplying factor is utilized for both faces of windows and doors.
- a. For framed, battened, panelled, braced, etc: one surface area is used (for both sides) x 2.25.
- b. Fully glazed: one surface area (for both sides) x 1
- c. Partly glazed and partly panelled: one surface area (for both sides) x 2
- d. For Flush doors: one surface area (for both sides) x 2
- e. Venetian: 3 cone surface area (for both sides).
- f. For grills, Iron bars in windows: area of clear openings in-between frames x 1.
10. Electrification, Sanitary and Water Supply Works:
8% of the estimated building cost is taken into account for sanitary and water supply work. 8% of the estimated building cost is allocated to electrification.
Section 4: Labour Safety and Welfare Laws
a. Explain briefly the procedure of pre-qualification of contractors. State its advantages and drawbacks. List the main points to be considered while pre-qualifying the contractors.
Ans. A. Procedure of Per-qualification:
- 1. Advertisement and Notification: It is the employer’s responsibility to advertise the Invitation for Prequalification (IFP) on the ADB website as well as in:
- i. An everyday newspaper published in the borrower’s nation (at least one English-language newspaper, if available)
- ii. An internationally known and freely website in English.
- 2. Preparing and Issuing a Prequalification Document:
- i. Preparing and distributing the pre qualification paperwork are the employer’s responsibilities.
- ii. The Employer shall Prequalify Bidders in accordance with the Standard Procurement Document of ADB (SPQD).
- iii .The employer must use the published version of the SPQD when creating the prequalification document, without deleting or adding anything to Section 1-Instructions to Applicants (ITA).
All information and data particular to each individual prequalification process must be provided by the employer in the following sections of the prequalification document:
Section 2 Application Data Sheet
Section 3 Qualification Criteria
Section 4 Application Forms
Section 5 Eligible Countries
Section 6 Scope of Contract
- iv. The employer shall allow applicants a minimum period of 42 days to:
- a. Study the prequalification document,
- b. Prepare complete and responsive applications, and
- c. Submit their applications.
- 3. Preparation and Submission of Applications:
- i. The applicant is solely responsible for the preparation and submission of its application.
- ii. During this stage, the employer shall:
- a. Promptly respond to requests for clarifications from applicants and amend, as needed, the prequalification document; and
- b. Amend the prequalification document only with the prior approval of ADB.
- 4. Opening and Evaluation of Applications:
- i. The employer must assign qualified personnel to carry out the application evaluation.
- ii. Evaluation errors may eventually lead to complaints from applicants, necessitating a re-evaluation of the applications, resulting in delays and resource waste.
- iii. The employer, in observance of best practices, shall:
- a. Maintain strict confidentiality throughout the evaluation process,
- b. Reject any attempts or pressures to distort the outcome of the evaluation. including fraud and corruption,
- c. Strictly apply only and all of the qualification criteria specified in the prequalification document; and
- d. Notify all applicants in writing of the names of those applicants who have been prequalified.
- 5. Updating and Confirmation of Bidder’s Qualifications:
- i. Information pertaining to a bidder’s eligibility, pending litigation, and financial situation shall be updated during bidding.
- ii. Additional qualifying requirements not examined during prequalification such as:
- a. Financial resources and current contract commitments.
- b. Equipment to be allocated for the particular contract.
- c. Personnel to be fielded for the particular contract.
Advantages:
- i. Enhances participation of serious contractors (since unqualified bidders are excluded).
- ii. Reduces high cost of bidding.
- iii. Gives early warning of competition potential.
- iv. Reduces complaints of disqualified bidders.
- v. Gives “Peace of Mind” to Employers.
- vi. Borrower able to assess interest of qualified firms.
- vii. Identifies potential conflict of interest (contractors with business association with consultants).
- viii. Reduces time in evaluating bids from unqualified bidders.
- ix. Reduces potential for controversy.
- x. Early Detection of Employer’s capacity to manage procurement.
Disadvantages:
- i. Increases procurement lead time.
- ii. Review of all application is mandatory whereas post-qualification requires review of only winning bid.
- iii. Possibility of collusion.
B. Main Points: Following are points to be considered while pre qualifying the contractors:
- 1. His financial strength.
- 2. His past experience in executing projects.
- 3. Number of technical personnel.
- 4. Construction, plant and equipment, and
- 5. Other considerations such as quality control standards, ISO certifications, and so on.
b. Classify the labour safety and welfare laws ? Explain them.
Ans. Following are laws/act related to labour safety and welfare:
- 1. Payment of Wages Act:
- i. This act has to do with paying wages. This law was put into place to control things like fines and wage payments.
- ii. This statute mandates that wages be paid on time each month, and if a person’s employment is terminated, his pay must be resolved within two days of the termination.
- 2. Minimum Wages Act:
- i. This act makes provisions for the establishment of a minimum wage that must be paid by law in the establishment.
- ii. In accordance with this act, several minimum rates may be established depending on the type of work, the employees, adults, permanent employees, or apprentices and the location of the job.
- 3. Factories Act:
- i. This legislation addresses health, safety, welfare, working conditions, annual leave, accidents, and any fines.
- ii. In terms of health, precautions must be taken to ensure that the workspace is kept clean, trash is properly disposed of, there is adequate ventilation, and the temperature is acceptable for working.
- iii. The typical working week consists of no more than 48 hours, with a maximum of 8 hours each day, including a half-hour lunch break.
- iv. If the employee works on a holiday, compensatory time off must be granted. Over time, salaries increase by two times the normal rate.
- v. Women workers should be employed only from 6 a.m. to 7 p.m.
- vi. In case of accident, proper compensation is to be paid as per the provision.
- 4. Contract Labour (Regulation and Abolition) Act, 1970 (Amended 1986):
- i. This statute includes provisions for bettering contract labour conditions.
- ii. In accordance with this Act, contractors are required to register themselves and acquire certificates of registration.
- iii. Restrooms, adequate ventilation, lighting, water supply, and sanitary facilities are among the welfare and health provisions that must be offered to contract labourers.
- iv. This act also covers first aid facilities and washing.
- v. Wages for each employee must be paid within the allotted time frame.
- 5. Workmen’s Compensation, Act, 1923 (Amended-1984):
- i. This act seeks to provide workers with social security. Whenever an accident occurs while a worker is on the job, compensation must be paid, and the amount depends on how serious the event is.
- ii. Under this act, financial relief is given in the following cases:
- a. In case of death,
- b. On account of occupational diseases,
- c. For permanent/partial disablement, and
- d. Half-monthly payments for temporary disablement.
- 6. The Trade Union Act, 1926:
- i. A trade union is a group of people who came together primarily to govern the interactions between employers and employees.
- ii. A trade union can be created with a minimum of 7 employees.
- iii. The union must register with the trade union registrar in order to operate. The pertinent information, such as the name and address. Before registering, the union’s goals, dues structure, and other details must all be agreed upon.
Section 5: Concept of Float and Slack
a. A small project is composed of nine following table:
Activity | t0 | tp | tm |
1-2 | 5 | 10 | 8 |
1-3 | 18 | 22 | 20 |
1-4 | 26 | 40 | 33 |
2-5 | 16 | 20 | 18 |
2-6 | 15 | 25 | 20 |
3-6 | 6 | 12 | 9 |
4-7 | 7 | 12 | 10 |
5-7 | 7 | 9 | S |
6-7 | 3 | 5 | 4 |
i. Find the expected task time and their variance.
ii. Earliest and latest expected time of each node.
iii. Critical path.
Ans. Given: Table.
To Find: Expected task time and their variance, earliest and latest expected time of each node and Critical path.
1. Network:
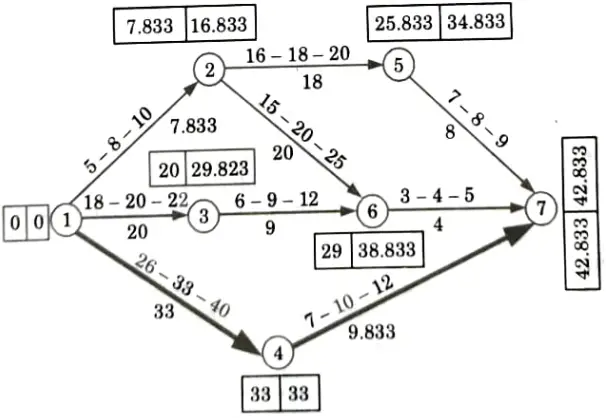
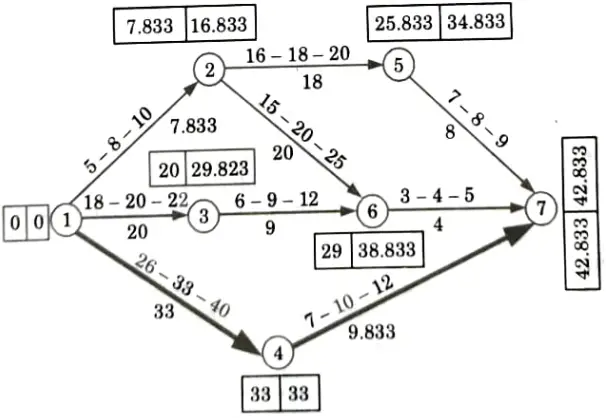
2. Calculation Table:
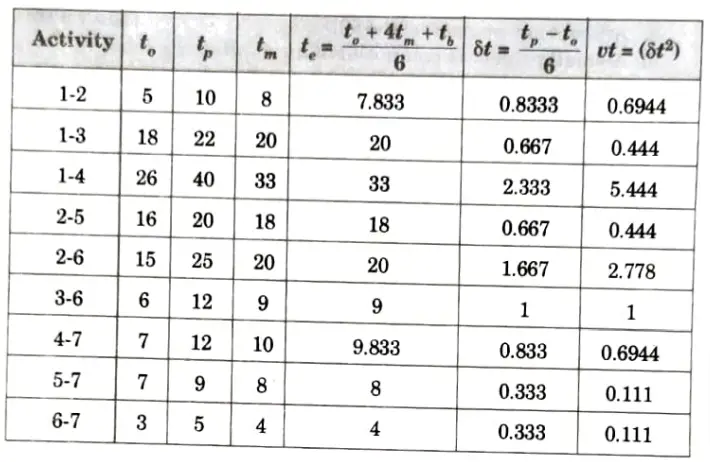
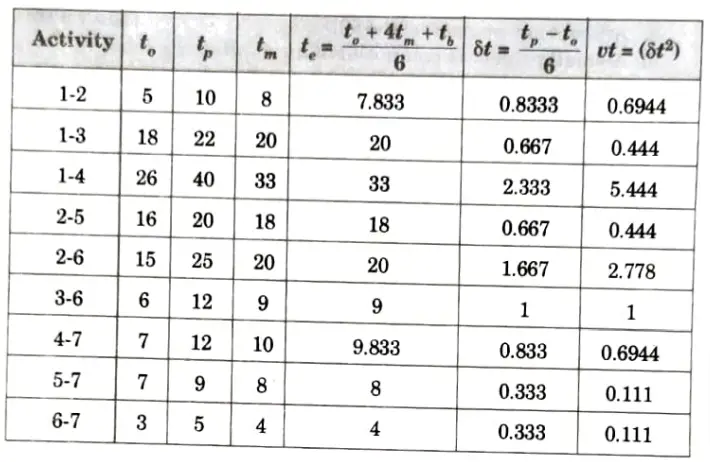
3. Critical path = 1 – 4 – 7
4. Expected task time = 33 + 9.833= 42.833 units
5. Variance of project = Variance along critical path,
= 5.444 + 0.6944 = 6.1384 units
b. i. Explain the concept of float and slack. Distinguish between the free, independent and interfering floats.
ii. Explain the three time estimates that are used in PERT. How are the expected duration of a project and its standard deviation calculated ?
Ans. i. 1. Slack:
i. Slack is amount of time that a task in a project network can be delayed without causing a delay to subsequent tasks and project completion data.
ii. The difference between TE and TL of an event is called the slack of that event.
Slack = TE – TL
2. Float:
i. Float denotes the flexibility range within which the activity start and finish times may fluctuate without affecting the total project duration.
ii. The float is similar to ‘slack’ in PERT. The difference is that float is associated with the activity times while slack is with event times.
Types of Float: Following are the various types of float:
1. Total Float:
i. It is the time span by which the starting or finishing of an activity can be delayed without affecting the overall completion time of the project.
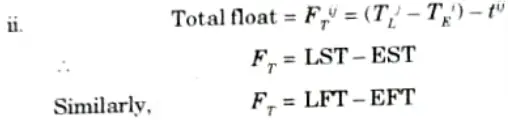
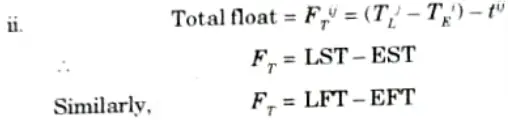
2. Free Float:
i. Free float is that duration by which an activity can be delayed without delaying any other succeeding activity. Free float is a portion of the total float.
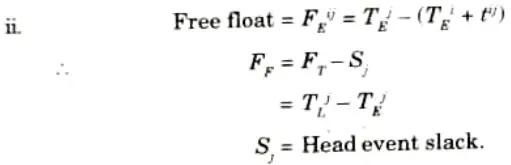
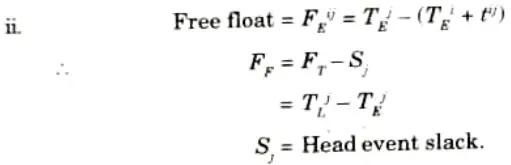
3. Independent Float:
i. If the previous activity wraps up as late as possible and the following activity gets underway as soon as possible, then the additional time is accessible.
ii. The independent float is a part of the free float.
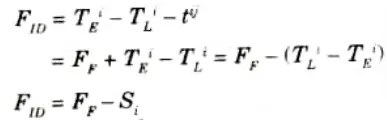
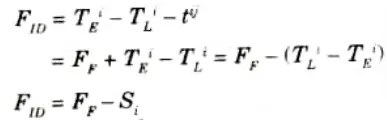
4. Interfering Float:
i. It is the difference between the total float and free float. This is equal to the head event slack.
ii. This is the potential downstream difference.
FIT = FT – PF = FT – (FT – SI)
FIT = SI
ii. There are three different estimates of activity duration in PERT:
1. Optimistic, 2. Pessimistic and 3. Most Likely.
1. Optimistic Time: It expressed as ‘to’ represents estimate of minimum possible time by which an activity can be completed assuming that everything is in order according to the plan and there can be only minimum amount of difficulty.
2. Pessimistic Time: It expressed as ‘tp’ represents estimate of maximum possible time by which an activity can be completed assuming that things may not be in accordance with the plan and there can be incidence of difficulties in carrying out the activity.
3. Most Likely Time: It expressed as ‘tm‘ represents estimate of time for completion of an activity, which is neither optimistic nor pessimistic, assuming that things should go in a normal way, and if the activity is repeated several times, in most of the cases, it will be completed in time represented by t.
4. The expected mean time (te) (duration) of a project is calculate by formula,
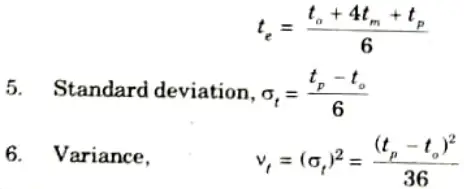
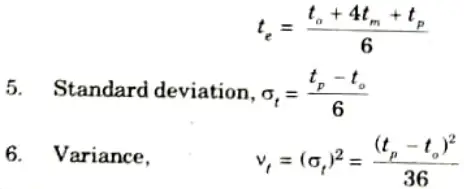
Section 6: Heavy Hauling Equipment Vehicles
a. What are the various types of heavy hauling equipment vehicles ? Also write in brief, their relative advantages and disadvantages.
Ans. A. Hauling Equipment:
- 1. Haulage of large construction equipment carriage and disposal of excavated earth transportation of building materials.
- 2. Haulers may operate on the roadways or railways.
B. Types of Hauling Equipments: Following are the various types of hauling equipments:
- 1. Side or Rear Dump Trucks:
- i. They are heavy duty trucks with a sturdy body that is hinged on the truck chassis at the rear end and one side, respectively, and can be fitted to the rear in the case of a rear dump and to the hinged side in the case of a side dump using hydraulic jacks.
- ii. These trucks can haul wet clay, sand, gravel, quarry rocks, and other materials.
- iii. They are also used for earth shifting.
- iv. The sort of dump truck used for a certain project is determined by the soil conditions.
- 2. Bottom Dump Trucks:
- i. They are similar to semi-trailers in that their front is supported by the carrying tractor’s rear and their rear is supported by their own wheels.
- ii. The truck’s body remains in place, and the material is discharged through its bottom after two longitudinal gates are opened.
- iii. The gates are hinged to the body’s side.
- iv. These trucks are appropriate for hauling free-flowing materials such as sand, gravel, dry soil, hard clay, and so on.
- 3. Dumpers:
- i. Dumpers are high speed pneumatic wheeled trucks.
- ii. They have short chassis and strong bodies.
- iii. Loading, hauling and dumping is done very fast as compared to other equipment.
- iv. Suitable for short hauls on rough roads, especially where a shuttle movement is required.
- 4. Tractors:
- i. Tractors are multi-purpose machines used mainly for pulling and pushing the other equipment.
- ii. Tractors may be classified as:
- a. Crawler Type Tractor: Used to transport bulldozers and scrapers. The crawler includes a chain, which allows these tractors to be quite successful even on loose or muddy terrain. Normally, the speed of this type does not surpass 12 kmph.
- b. Wheel Type Tractor: The engine is mounted on four wheels. The main advantage is higher speed, sometimes exceeding 50 kmph, it is used for long-distance hauling and good roads.
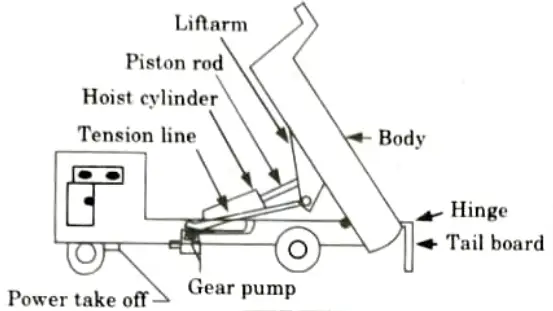
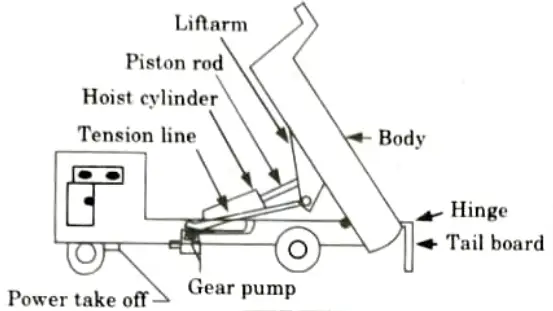
B. Advantages and Disadvantages :
a. Side or Rear Dump Truck:
Advantage:
1. The key advantages of the side dump are that it allows rapid unloading.
Disadvantages:
1. Maneuverability is not good for confined unload.
b. Bottom Dump Trucks:
Advantage:
1. The biggest advantage of bottom dump truck is the ability to lay material in a wind row.
Disadvantage:
1. A primary disadvantage to this design is that it is not good for large or bulky items.
c. Dumpers:
Advantage:
1. Better Productivity: It offers on increased rate of productivity by moving unnecessary items from the construction sites.
2. Impeccable Services: It an be used effectively to transport all heavy construction materials quickly and effortlessly.
3. Various Sizes: These trucks are available in a huge range of sizes.
Disadvantage:
1. It is a lot larger than other trucks so needs more storage space and room to maneuver.
2. Does not perform so well in extreme weather conditions.
d. Tractors:
Advantages:
1. Can pull heavy loads.
2. They are built to last many years, and are able to withstand harsh conditions.
Disadvantages:
1. Lack speed.
2. Require careful maintenance.
b. Explain the following types of equipments:
i. Hoisting Equipments.
ii. Conveying Equipment.
iii. Transporting Equipments.
iv. Hauling Equipments.
v. Excavating Equipments.
Ans. i. Hoisting Equipments: Hoisting is the process of raising a cargo. Hoisting equipment lifts the cargo from one area to another and keeps it suspended during the transfer.
ii. Conveying Equipment:
- i. Moving stuff from one location to another using a stationary structure.
- ii. Transports material in a continuous stream using a distinguishing characteristic such as an unending chain or belt.
- iii. When the equipment conveys horizontally, it is referred to as a conveyor, and when it conveys vertically, it is referred to as a lift.
- iv. Conveying is mostly utilised in mining, construction, and a few other industries.
- v. Conveyors are mostly used in the construction industry for concreting.
iii. Transporting Equipments: They are heavy duty vehicles with a sturdy body that is hinged on the truck chassis at the rear end and one side, respectively, and can be attached to the rear in the case of a rear dump and to the hinged side in the case of a side dump using hydraulic jacks.
iv. Hauling Equipments:
- 1. Haulage of large construction equipment carriage and disposal of excavated earth transportation of building materials.
- 2. Haulers may operate on the roadways or railways.
v. Excavating Equipments: Following are the excavating and earth moving equipment:
- 1. Power Shovel: The track system, cabin, cables, rack, stick, boom foot-pin, saddle block, boom, boom point sheaves, and bucket are the basic components of a power shovel.
- 2. Back Hoe: It is also known as hoe, back shovel and pull shovel.
- 3. Drag Line: The drag line gets its name from the visible activity of dragging the bucket against the material to be excavated.
- 4. Clam Shell: This is so named due to resemblance of its bucket to a clam which is like a shell-fish with hinged double shell.
- 5. Trenching Machine: Trenchers are the equipments used for excavating trenches or ditches of variable width and depth.
- 6. Scrapers: Unique machine for digging and long-distance hauling of plough able materials.
- 7. Bulldozer: The heavy blade attached to the tractor pushes the material from one place to another.
Section 7: Engineering Economic Analysis
a. Calculate the optimum duration and the cost associated with it, if the project overhead cost are @ Rs 250 per day. Also draw the least cost network. Table gives the data about durations costs if various activities of the network.
Activity | Normal Duration (Days) | Normal Cost (Rs). | Crash Duration (Days) | Crash Cost (Rs). |
1-2 | 9 | 8000 | 6 | 9500 |
2-3 | 5 | 5000 | 3 | 5500 |
Ans. Given : Overhead cost =250 Rs/day, and table.
To Find: Optimum cost and duration and draw least cost network.
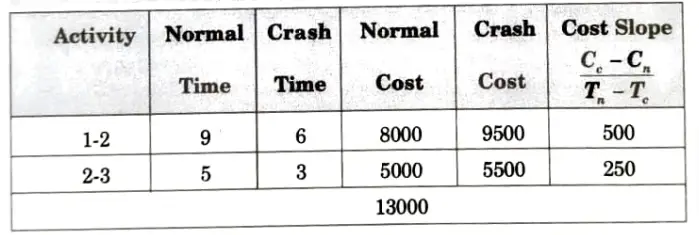
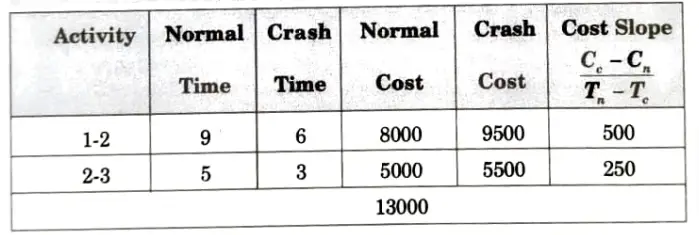
1. Least Cost Network:


2. Project duration = 9 + 5 = 14 days
3. Total normal cost = 13000 + 0 + 13 x 250 = 16250 Rs
4. Crash time = 6 + 3 = 9 days
5. Activity 2 – 3 crashed by 2 days and activity 1 – 2 crashed by 3 days
6. So, project cost now
= 16250 + 2 x 250 + 3 x 500 – 5 x 250
= 17000 Rs
7. Optimum cost = 17000 Rs
8. Optimum duration = 9 days
b. Discuss the following methods used in engineering economic analysis for evaluating and comparing alternatives:
i. The present worth method.
ii. Future worth method.
iii. The annual equivalent method.
iv. Rate of return method.
Ans. i. The Present Worth Amount: The method is described as follows:
- 1. For each choice, separately indicate all expenses and benefits at the relevant point in time in the form of cash flow. Depict expenses (costs) with downward arrows and benefits or savings with upward arrows. In the algebraic statement, the + sign represents expenses and the – sign represents benefits.
- 2. Using suitable interest calculations, shift the money at zero time and calculate the total present worth of each choice and compare them.
There may be two cases.
i. Case I: When service life of each alternative is same.
Item no. (2) will clearly indicate which alternative has lower present worth. The alternative having lower present worth is economically accepted.
ii. Case II: When service life of alternatives is different.
The cycle of item no. (2) is repeated till the common service life is obtained. The common life is taken as the LCM value of the given lives. The overall present worth of alternatives are obtained and then compared for the selection of economical alternative.
ii. Annual Equivalent Amount:
1. In this method, cash flow is converted into a series of equal annual amount by first calculating the present worth amount for the original series and then multiplying it with capital recovery factor
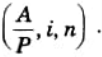
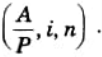
2. The comparison is made by seeing the annual equivalent amount of each alternative.
iii. The Capitalized Amount/ Future Worth Method:
1. The annual equivalent amount obtained is assumed to extend for in-finite period and the capitalized amount is obtained by using


2. The equal annual sum for replacement and maintenance costs is computed and added to the original cost of the alternative.
iv. Rate of Return Method:
- 1. It is defined as the interest rate that decreases the present value of a series of receipts and disbursements to zero for each choice.
- 2. In economic terms, the core concept of rate of return is that it is the rate of interest generated on an investment’s unrecovered balance so that the unrecovered balance is zero at the end of the investment’s life.
- 3. In general, calculating the rate of return needs trial and error until the I can be interpolated. The most frequent conversion is a ‘+’ sign for cash inflows and a ‘-‘ sign for cash outflows.
6 thoughts on “Quantity Estimation and Construction Management: Solved Aktu Question Paper”