B.Tech AKTU Quantum Book will introduce you to the world of Industrial Engineering. To thrive in this profession, access crucial notes, repeated questions, and helpful insights. Unit-1 Overview of Industrial Engineering
Dudes 🤔.. You want more useful details regarding this subject. Please keep in mind this as well. Important Questions For Industrial Engineering: *Quantum *B.tech-Syllabus *Circulars *B.tech AKTU RESULT * Btech 3rd Year * Aktu Solved Question Paper
Q1. What do you mean by production ? Explain production system.
Ans. A. Production:
- 1. It is any system or process created to convert a specific set of output elements, such as finished products and services in the right amount and quality, into a set of input elements, such as men, materials, capital, information, and energy.
- 2. The creation of things, whether through the transformation of raw materials or the assembly of numerous small components, is the essence of production.
B. Production System:
- 1. A production system is a deliberate act of production.
- 2. A production system uses land, labour, machinery, capital, and materials to produce things under efficient management.
- 3. A production system is a method that effectively transforms input components into usable output goods through an ordered process.
Q2. Differentiate between intermittent and continuous production process.
Ans.
S. No. | Intermittent Production Process | Continuous Production Process |
1. | Same product is not produced continuously. | Same product is produced continuously. |
2. | Items produced for order. | Items produced for stock. |
3. | Production process is flexible. | Process is not flexible. |
4. | Equipment used for limited time. | Regular use of equipment. |
5. | Wide range of products can be produced. | Only particular type of product is produced. |
6. | Smaller scale of production. | Large scale of production. |
7. | Planning and control operations are complicated and tedious. | Planning and control operations are simple and easy. |
8. | Capital investment may be low. | Capital investment is high. |
9. | Change in location is easy. | Change in location is difficult. |
10 | Product and process are not standardized. | Product and process are standardized. |
Q3. What are the factors affecting productivity.
Ans. Following are the factors affecting productivity:
- a. Technological Development: The amount of technological growth in every industry is determined by technical elements such as the degree of mechanization, technical know-how, raw materials, layout, and the methods and techniques of work.
- b. Individual Factors: Individual characteristics like knowledge, skill, and attitude also have an impact on an industry’s production.
- c. Organization Factors: Organizational factors include different actions the organization has taken to maintain better labour relations, such as delegating and decentralizing authority, participative management, worker involvement in management, organizational effectiveness, proper personnel policies relating to selection, placement, promotion, wage salary levels, incentives, merit rating, job evaluation, training and provision for two-way communication, supervision, etc. These aspects affect motivation as well.
- d. Work Environment: Industrial psychologists and human engineers have underlined the significance of a healthy work environment and comfortable working circumstances. A better work environment guarantees the best comfort at work through better lighting and ventilation, enhanced safety equipment, reduced noise, the introduction of appropriate rest breaks, etc.
Q3. Explain facility location or plant location. Write the factors considered for the selection of a site.
Ans. A. Facility Location or Plant Location:
- 1. Choosing a suitable location for the plant or factory to begin operations is referred to as choosing a plant location.
- 2. The issue of plant location appears when a new factory is established or when an existing facility is expanded.
- 3. Plant location involves two main activities:
- i. Selection of suitable geographic region.
- ii. Selection of specific site in that region.
B. Factors Considered for the Selection of a Site: Following factors are considered while selecting a site for a plant:
- a. Nearness to Raw Material: The cost of transportation will be significant if the raw materials are large and weighty. So, it is usually preferable to position the facility close to the raw material supply.
- b. Land: The choice of site is influenced by the topography, available space, cost, drainage and other amenities, likelihood of floods, earthquakes, etc.
- c. Transport Facilities: Transporting raw materials and finished commodities typically involves significant financial outlays. A suitable mode of transportation is chosen based on the nature and dimensions of the raw materials and finished items (road, rail, water or air). The location of the plant is chosen accordingly.
- d. Availability of Labour: The necessary number of workers must be close to the plant. They must be dependable and have the proper attitude towards their jobs. The price of the labour should be fair.
- e. Availability of Fuel and Power: Electricity must be available continuously in the right quantities and at fair prices. In order to reduce the expense of transporting fuel, steel plants are typically situated close to coal fields.
- f. Other Factors:
- 1. Political and social environment,
- 2. Presence of supporting industries and services nearby,
- 3. Availability of hospitals, schools, marketing centres, banks, post offices etc.,
- 4. Housing facilities, and
- 5. Security.
Q4. What is line balancing? Explain it.
Ans.
- 1. In a layout, balancing the manufacturing or assembly line, particularly in product layout, is referred to as line balance.
- 2. That might happen because each machine in the sequence has a different production capacity.
- 3. Assume, for instance, that there are three workstations with respective production rates of 25, 50, and 100 items per hour: A, B, and C.
- 4. Fifty percent of the time won’t be spent at workstations B and C. Such a design needs to be balanced because it is unbalanced.
- 5. In order to balance the line, the production capacities of workstations A and B must be increased to correspond with the work station with the highest capacity.
- 6. This will enable all stations to operate at their full potential. Hence, setting up four machines at workplace A and two at place B will achieve line balancing for 100 units per hour at workplace A.
- 7. The major goal is to evenly divide duties across the workstations in order to reduce both the amount of time that people and machines are idle.
Q5. Discuss the production equipment and tool selection for the component shown in Fig. undercut diameter is 12 mm.
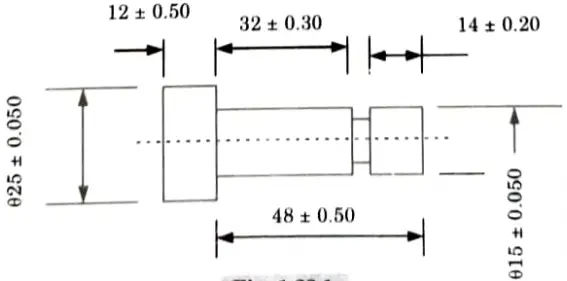
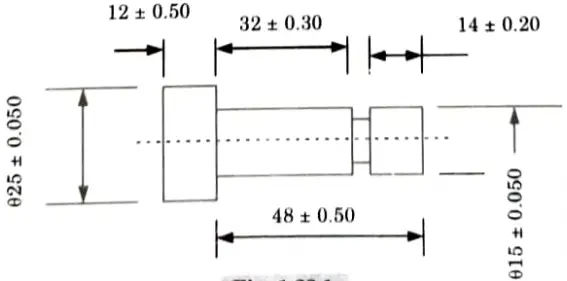
Ans. Production equipment and tool selection for the component is as follows:
a. Evaluation of Process and Machine Selection:
- 1. The recognised process is turning, and the machine tool is a small bench lathe, as specified in the problem. This restricts our options to the machine shop’s stock of tools.
b. Analysis of Machining Operations:
- 1. The operations identified are facing, roughing, finishing and parting off. From this, two specific tools can be identified:
- i. Turning/facing tool- facing, roughing and finishing;
- ii. Parting off tool- parting off
c. Analysis of Workpiece Characteristics:
- 1. Since the workpiece is made of brass, HSS tooling is more than enough for performing all operations. This is a result of the great degree of machinability of brass.
- 2. There are, however, two concerns to take into account in terms of the geometry of the workpiece and the tool. A left-handed tool will not be able to finish the middle arc of the part in terms of facing and roughing out.
- 3. There are two choices that can be taken into account. The first is to create the first half of the arc using a left-handed tool and the second half with a right-handed tool.
- 4. But, applying a contouring tool to the entire arc would be considerably easier. Moreover, a contouring tool will be needed for the part’s left-end chamfered groove.
- 5. Because this requires the fewest tools, it makes logical to utilize the contouring tool for both features, rake angles permitting.
d. Tooling Analysis:
- 1. From the above stages, the following tooling list and operation description can be generated:
- i. Facing: left-hand turning tool.
- ii. Roughing: left-hand turning tool.
- iii. Finishing: contouring tool.
- iv. Parting off: parting-off tool.
- v. Face the end and rough out the excess material with the left-hand turning tool.
- 2. The majority of the finish turning can be carried out with the left-hand turning tool.
- 3. However, the contour tool will be used to mill the radius and the chamfered groove, and then the splitting off tool will be used to cut the part from the billet.
Q6. Discuss flexible manufacturing.
Ans.
- 1. A highly automated GT machine cell is referred to as a flexible manufacturing system (FMS).
- 2. It is made up of a collection of processing workstations (often CNC machine tools) coupled by an automated material handling and storage system and run by a distributed computer system.
- 3. The FMS is referred to as flexible because it can process numerous distinct part types concurrently at separate workstations, and the mix of part styles and production volumes can be changed in response to shifting demand patterns.
- 4. The mid-variety, mid-volume production range is not appropriate for the FMS.
- 5. The term Flexible Machining System is occasionally abbreviated as FMS. The machining process currently represents the FMS technology’s largest application field.
- 6. However, it seems appropriate to interpret FMS in its broader meaning allowing for a wide range of possible applications beyond machining.
- 7. A FMS relies on the principles of group technology.
- 8. No production system can be totally adaptable. The variety of components or goods that can be produced in an FMS is constrained.
- 9. In light of this, a flexible manufacturing system is made to create parts (or products) in a variety of shapes, sizes, and ways.
- 10. Flexible Automated Manufacturing System might be a better name for FMS.
- 11. The adjective “automated” would set this form of production technology apart from other flexible but non-automated manufacturing methods, such as a manned GT machine cell.
- 12. The adjective “flexible” would set it apart from other highly automated but rigid production systems, such a traditional transfer line.
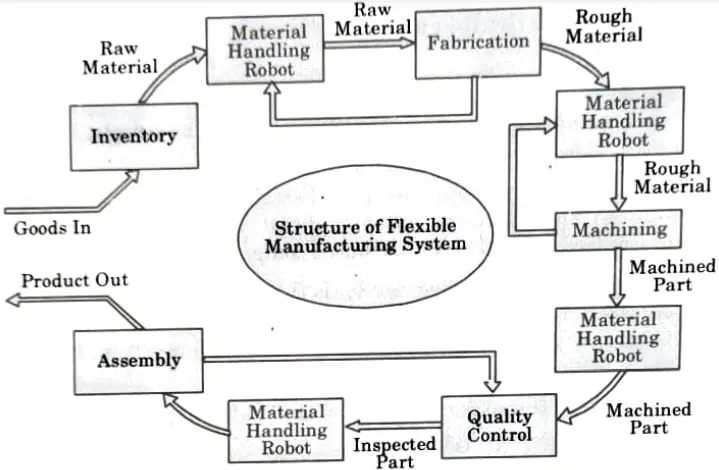
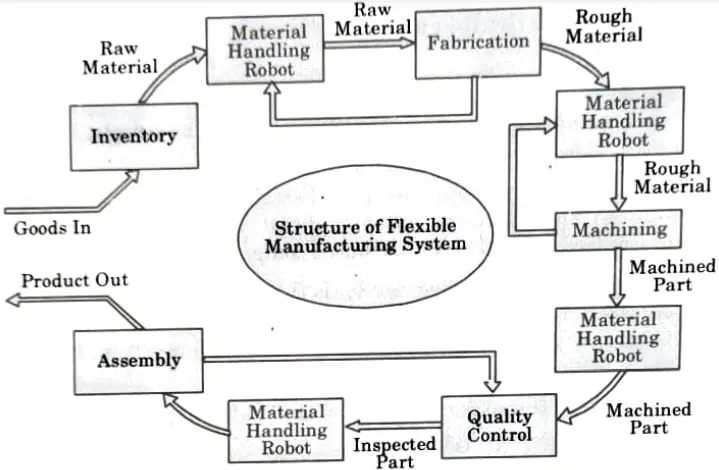
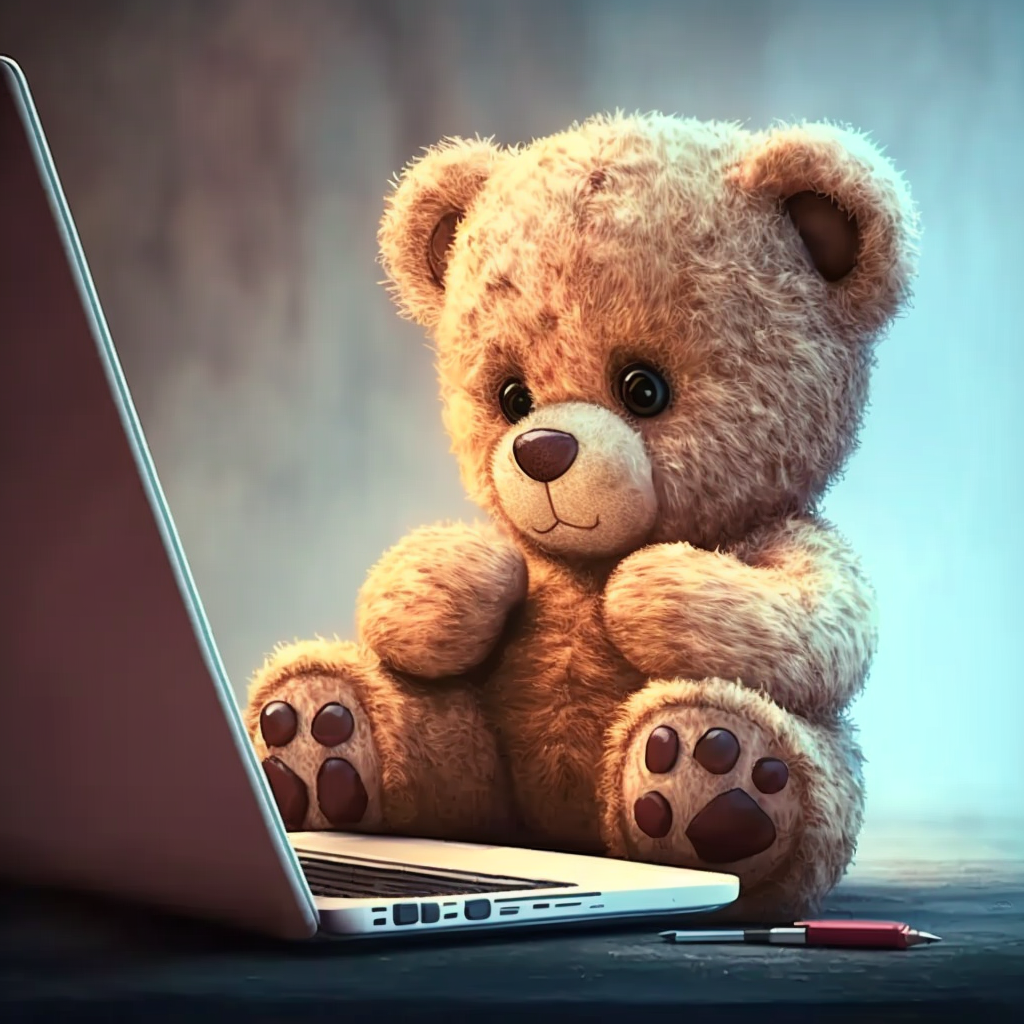
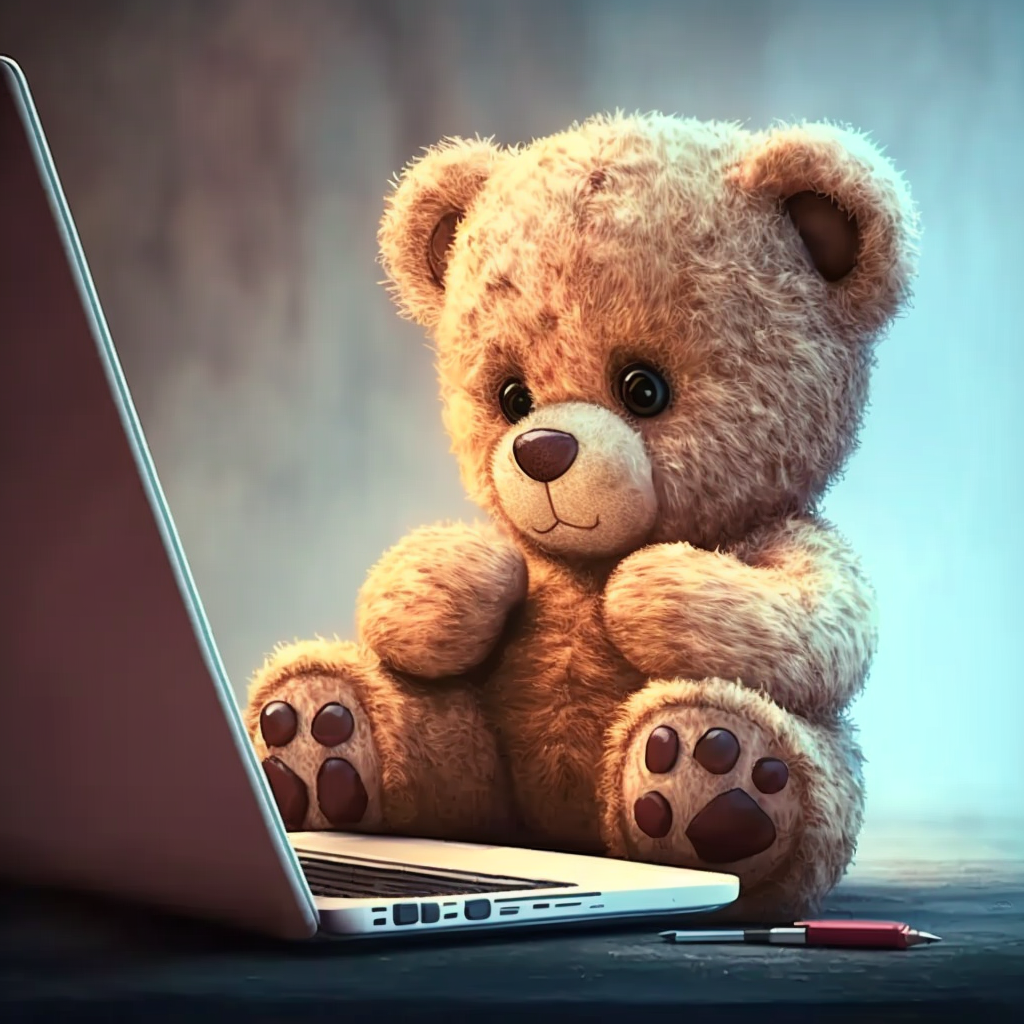
Important Question with solutions | AKTU Quantums | Syllabus | Short Questions
Industrial Engineering Btech Quantum PDF, Syllabus, Important Questions
Label | Link |
---|---|
Subject Syllabus | Syllabus |
Short Questions | Short-question |
Question paper – 2021-22 | 2021-22 |
Industrial Engineering Quantum PDF | AKTU Quantum PDF:
Quantum Series | Links |
Quantum -2022-23 | 2022-23 |
AKTU Important Links | Btech Syllabus
Link Name | Links |
---|---|
Btech AKTU Circulars | Links |
Btech AKTU Syllabus | Links |
Btech AKTU Student Dashboard | Student Dashboard |
AKTU RESULT (One VIew) | Student Result |