Use Aktu’s Quantum Notes to increase your knowledge of Concrete Technology. Learn essential ideas and answers to frequently asked questions to succeed in your B.Tech courses. Success made simple! Unit-1 Cement Production and Aggregates
Dudes 🤔.. You want more useful details regarding this subject. Please keep in mind this as well. Important Questions For Concrete Technology: *Quantum *B.tech-Syllabus *Circulars *B.tech AKTU RESULT * Btech 3rd Year * Aktu Solved Question Paper
Q1. What is cement ? Also give its composition.
Ans. A. Cement:
- 1. Cement is an inorganic material that has been finely ground; when combined with water, it creates a paste that sets and hardens as a result of hydration reactions and processes, and after it has hardened, it retains its strength and stability even in the presence of water.
- 2. A mixture of calcareous, siliceous, argillaceous, and other materials constitutes cement.
B. Chemical Composition: Cement has the following approximate chemical composition:
- 1. The major constituents are:
- i. Lime (CaO): 60-63 %
- ii. Silica (SiO2): 17-25 %
- iii. Alumina (Al2O3): 03-08 %
- 2. The auxiliary constituents are:
- i. Iron oxide (Fe2O3) :0.5 – 06 %
- ii. Magnesia (MgO): 1.5 – 03 %
- iii. Sulphur trioxide (SO2):01-02 %
- iv. Gypsum : 01 to 04 %
Q2. Explain manufacturing processes of the cement with neat diagram. Give comparison between wet and dry process of manufacturing.
Ans. Manufacturing Processes: Following are the steps of manufacturing of cement:
A. Make Clinkers: In this step, the raw material is converted into fine powder and it is done by following two processes:
- 1. Dry Process:
- i. In this method, calcareous materials like limestone (calcium carbonate) and argillaceous materials like clay are crushed separately to a fine powder without the use of water before being combined in the proper ratios.
- ii. After adding water to make a thick paste, it is then moulded into cakes, dried, and burned in kilns.
- iii. This procedure is typically applied when the raw materials are extremely robust and difficult.
- iv. Without the use of water, the raw ingredients are converted to powder in this process.
- 2. Wet Process:
- i. In this procedure, water is used to turn the raw ingredients into powder.
- ii. A ball mill, which is a rotating steel cylinder with hardened steel balls within, is used in this procedure to grind up the raw materials.
- iii. Steel balls grind the raw materials as the mill turns, creating slurry (liquid mixture).
- iv. After the slurry has entered storage tanks, the proper proportioning is carried out there.
- v. Using a wet process rather than a dry method can ensure that raw ingredients are properly composed.
- vi. This method is typically employed with soft raw materials because adding water makes complete mixing impossible.
- vii. Corrected slurry is then fed into rotary kiln for burning.
The actual purpose of both processes is to change the raw materials to fine powder.
B. Burning:
- i. Slurry that has been corrected is fed into a rotary kiln, which has a 150-500 foot length, a diameter of 8–16 feet, and a temperature setting of 18 up to 1500-1650 °C.
- ii. Slurry loses moisture at this temperature and congeals into tiny lumps before becoming clinkers.
- iii. Clinkers are cooled in another inclined tube similar to kiln but of lesser length.
C. Grinding:
- i. After being cooled to ambient temperature, the clinker is then ground as the last step in the process.
- ii. Grinding of clinker is done in large tube mills. After proper grinding gypsum (Calcium sulphate CaSO4) in the ratio of 01-04 % is added for controlling the setting time of cement.
- iii. Finally, fine ground cement is stored in storage tanks from where it is drawn for packing.
Comparison between Wet and Dry Process:
S. No. | Wet Process | Dry Process |
1. | Moisture content of the slurry is 35-50%. | Moisture content of the pellets is 12%. |
2. | The size of the kiln required to make cement is larger. | The size of the kiln required to produce cement is smaller. |
3. | The amount of heat required is higher, so the required fuel amount is higher. | The required quantity of heat is Less heat is needed, hence the amount is less. |
4. | Less economical. | More economical. |
5. | The basic components are simple to blend, making it possible to produce a more homogeneous product. | It is challenging to obtain homogeneous material since the process of blending raw components is difficult to manage. |
6. | The apparatus and equipment don’t require a lot of upkeep. | More maintenance is required for the machinery and equipment. |
Q3. What is hydration of cement ? Explain the process of hydration of cement.
Ans. A. Hydration of Cement:
- 1. Hydration refers to the reaction that occurs when cement and water are combined. Around 75% of cement is made up of both C3S and C2S.
- 2. The setting and hardening of cement is caused by the hydration of these chemicals.
- 3. As soon as cement and water come into contact, the hydration surface reaction begins. This reaction is exothermic.
- 4. Hydration keeps on so long as heat and moisture are present.
- 5. Gypsum and all four of Bogue’s chemicals are involved in the hydration reaction, which only requires a very small amount of water.
B. Following stages occurred in the process of hydration:
- 1. Stage 1: During over 15 minutes, a quick order heat generation occurs. When a particular threshold of critical concentrations is achieved, the surface releases calcium and hydrogen ions, which lead to the development of calcium hydroxide and calcium silicate hydroxide. The temperature affects the earliest reactions.
- 2. Stage 2: The cement is forced to become pliable for a period of two to four hours during this stage, which is typically the dormant phase. This response process tends to get slower.
- 3. Stage 3: As the silicate hydrates quickly and at a critical ion concentration, this is the acceleration phase. The time period is typically between 4 and 8 hours, during which the full hardening process is completed and the final set is released.
- 4. Stage 4: This phase is referred to as deceleration. An independent diffusion reaction results from the tendency of the reaction’s overall rate to slow down.
- 5. Stage 5: The temperature has less of an impact on the hydration stage during this period, which is known as the stable stage. The reaction process lasts for 12 to 24 hours and is continuous.
More often than not, the combined reaction of cement hydration is more efficient than the individual reactions of minerals. The hydration of cement can be broken down into a number of smaller components, and it has been found that the aluminate and ferrite phases typically react first before continuing to the silicate phase.
Q4. What are the advantages of pozzolana portland cement.
Ans. Advantages:
- 1. PPC is cost-effective because expensive clinker is replaced with less expensive pozzolanic material.
- 2. Improved permeability results from the conversion of soluble calcium hydroxide into insoluble cementitious products. As a result, it offers general endurance qualities, which are especially useful in hydraulic constructions and marine construction.
- 3. Unlike OPC, PPC does not make as much calcium hydroxide as it requires.
- 4. It produces decreased hydration heat, and that too at a slow rate.
- 5. Pozzolanic action and the fact that PPC is finer than OPC increase the pore size distribution and decrease microcracks at the transition zone.
- 6. Because to its finer texture and lower density, fly ash has a little larger bulk volume than OPC in a 50 kilogramme bag. As a result, PPC provides larger mortar volume than OPC.
- 7. If enough moisture is present for ongoing pozzolanic action, PPC has longer-lasting strength than OPC after a few months.
Q5. Briefly describe the physical mechanical and thermal properties of aggregates in concrete.
Ans. A. Physical Properties of Aggregate :
- 1. Grading: It is an aggregate’s particle-size distribution as measured by a sieve analysis with wire mesh sieves that have square holes.
- 2. Fineness Modulus: The fineness modulus serves as an expression for the outcome of aggregate sieve analysis.
- 3. Flakiness Index: It is the proportion of particles by weight in which the smallest dimension is less than three-fifths of the mean particle size.
- 4. Elongation Index: It is the proportion of particles by weight whose largest dimension exceeds 1.8 times their mean dimension.
B. Mechanical Prosperities of Aggregate:
- 1. Aggregate Crushing Value: It provides a comparative measurement of an aggregate’s resistance to crushing under a compressive load that is gradually applied.
- 2. Aggregate Impact Value: It provides a comparative measurement of an aggregate’s resistance to a sudden shock or impact.
- 3. Aggregate Abrasion Value: When an aggregate is rotated in a cylinder with an abrasive charge, it provides a relative measure of the resistance to wear.
C. Thermal Properties of Aggregate: Following are the thermal properties of aggregate:
- 1. Coefficient of Thermal Expansion: When aggregate thermal expansion increases, so does the concrete’s thermal expansion coefficient. The parent rock affects the aggregate’s coefficient of expansion.
- 2. Specific Heat: It is a measure of its heat capacity.
- 3. Thermal Conductivity: It is the ability of the aggregate to conduct the heat.
Q6. What tests are used to find out the shape of the aggregate?
Ans. There are mainly two types of test for finding the shape of aggregate, which are as follows:
A. Test for Determination of Flakiness Index:
- 1. The percentage by weight of aggregate particles whose thinnest dimension (thickness) is less than three-fifths of their mean dimension is known as the flakiness index. Sizes less than 6.3 mm are not eligible for the test.
- 2. A metal thickness gauge is used to do this examination.
- 3. Enough aggregate is removed to allow for the testing of at least 200 pieces of each fraction.
- 4. The thickness of each fraction is measured on the metal gauge one by one.
- 5. The weight of the samples used to weigh the total amount going through the gauge is accurate to within 0.1%.
- 6. The total weight of the material that passes through the several thickness gauges is used to calculate the flakiness index, which is expressed as a percentage of the sample’s overall weight.
B. Test for Determination of Elongation Index:
- 1. The percentage of particles in an aggregate with a maximum dimension (length) higher than 1.8 times their mean dimension is known as the elongation index.
- 2. Sizes smaller than 6.3 mm are not eligible for the elongation index.
- 3. A metal length gauge is used for this examination.
- 4. Enough aggregate is extracted to produce at least 200 pieces of each fraction that will be evaluated.
- 5. On the metal gauge, each fraction must be measured independently for length.
- 6. The entire amount held by the gauge length must be accurately weighed to within 0.1% of the test samples’ weight.
- 7. The total weight of the material maintained on the various length gauges, represented as a percentage of the total weight of the sample gauged, is what makes up the elongation index.
- 8. More than 15% of elongated particles are typically regarded as undesirable.
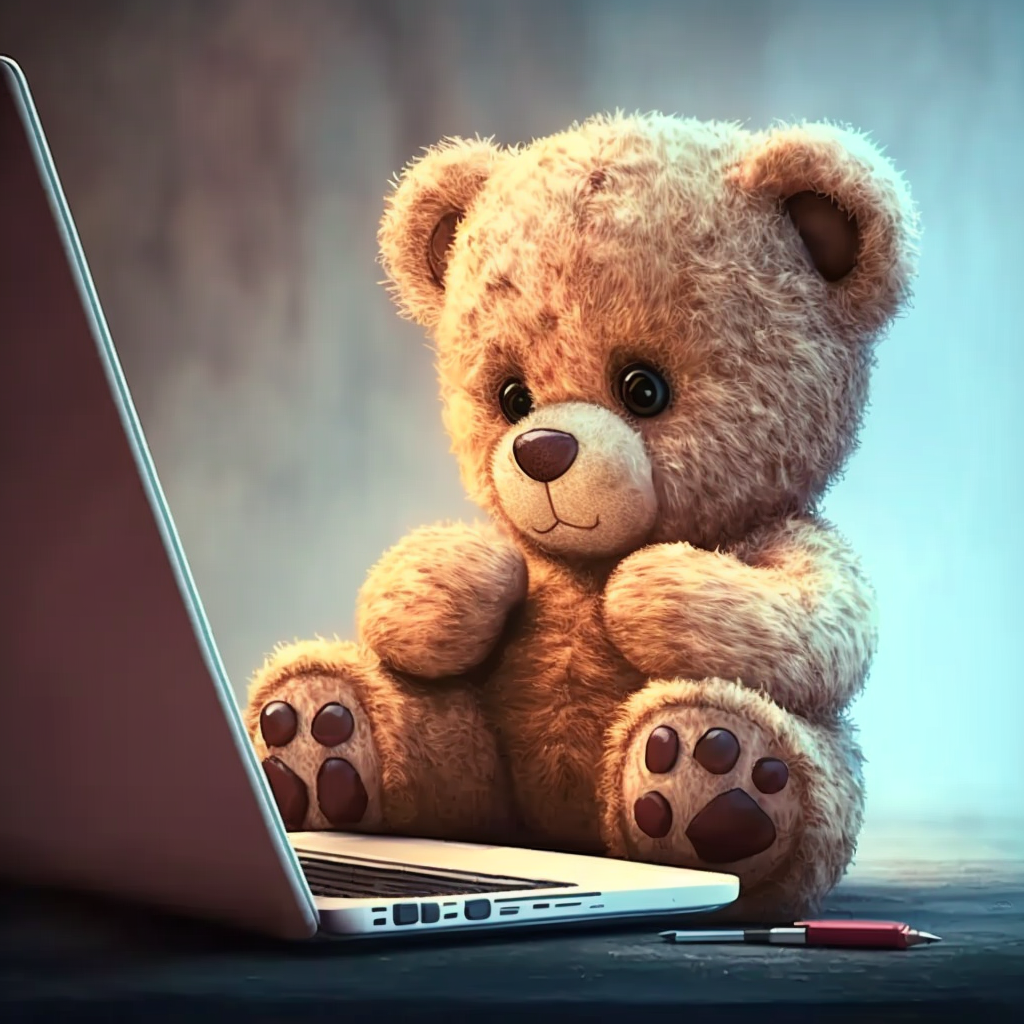
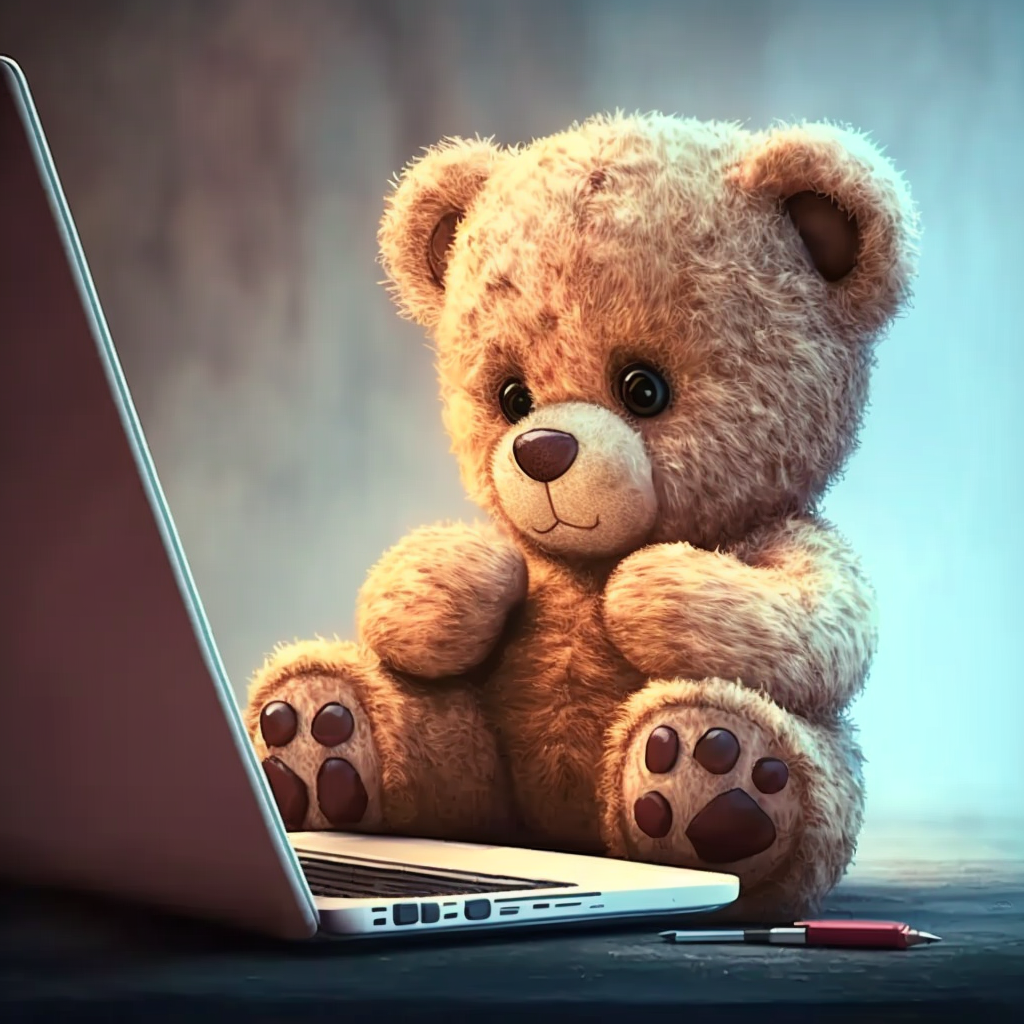
Important Question with solutions | AKTU Quantums | Syllabus | Short Questions
Concrete Technology Btech Quantum PDF, Syllabus, Important Questions
Label | Link |
---|---|
Subject Syllabus | Syllabus |
Short Questions | Short-question |
Question paper – 2021-22 | 2021-22 |
Concrete Technology Quantum PDF | AKTU Quantum PDF:
Quantum Series | Links |
Quantum -2022-23 | 2022-23 |
AKTU Important Links | Btech Syllabus
Link Name | Links |
---|---|
Btech AKTU Circulars | Links |
Btech AKTU Syllabus | Links |
Btech AKTU Student Dashboard | Student Dashboard |
AKTU RESULT (One View) | Student Result |