“With our AKTU question paper and solution, explore the world of Concrete Technology. Discover new information and understanding with these thorough notes on this fundamental building element.
Dudes 🤔.. You want more useful details regarding this subject. Please keep in mind this as well. Important Questions For Concrete Technology: *Quantum *B.tech-Syllabus *Circulars *B.tech AKTU RESULT * Btech 3rd Year
Section A: Concrete Technology Short Notes
a. List four Bogue’s compounds with their percentage in ordinary portland cement.
Ans. Bogue’s Compounds: The composition of portland cement is basically consist of four main compounds:
Percentage:
- 1. Tricalcium silicate, a well-burnt cement, is thought to be the best cementing substance. There is typically between 25 and 50 percent cement in it.
- 2. Around 25-40% (often around 32 percent) of cement is composed of dicalcium silicate.
- 3. Around 5-11% (often about 10.5 percent) of cement is made up of tricalcium aluminate.
- 4. Tetracalcium Alumino Ferrite accounts for 8-14% (often 9%) of cement.
b. Why the cement should not be allowed come in moisture contact?
Ans. The cement should not come into touch with moisture because of its hygroscopic nature; the cement absorbs moisture from the atmosphere very actively and hardens like stone, making it unsuitable for construction.
c. Why accelerators are added to concrete?
Ans. When added to concrete, mortar, or grout, these substances improve the rate of hydration of a hydraulic cement, shorten the time of set, or accelerate the pace of hardening or strength development.
d. Define silica fume.
Ans. Silica fume is a very fine pozzolanic substance made up of ultrafine, amorphous glassy spheres of silicon dioxide formed during the production of silica or ferro-silicon in an electric arc furnace at temperatures above 2000 °C.
e. What is durability of concrete?
Ans. 1. Concrete’s durability is described as its ability to withstand weathering, chemical attack, abrasion, or any other deterioration process.
2. When exposed to the elements, durable concrete will preserve its original form, quality, and serviceability.
f. Define M 45.
Ans. The letter M is followed by a number to represent the grade of concrete. The letter ‘M’ denotes the mix, while the number denotes the compressive strength of concrete in N/mm2 or MPa. M 45 indicates that the mix’s typical compressive strength is greater than 45 MPa.
g. What do you know about mix design of concrete ?
Ans. It is the process of selecting suitable elements for concrete and determining their proportions in order to make concrete with a specific minimum compressive strength, workability, and durability as economically as possible.
h. What is the effect of Ca (OH)2 in concrete?
Ans. Calcium hydroxide combines with sulphates in soils or water to generate calcium sulphate, which then reacts with C3A and causes concrete degradation. This is referred to as sulphate assault.
i. Define high strength concrete.
Ans. In comparison to traditional concrete, which has a compressive strength of less than 50 MPa, it has a compressive strength of up to 100 MPa. Ultrahigh strength concrete is defined as having a compressive strength more than 200 MPa.
j. Define ready mix concrete.
Ans. Ready Mix Concrete: Ready mixed concrete is described as concrete that has been mixed in a stationary mixer in a central batching and mixing plant or in a truck mixer and is delivered to the customer in a fresh state, either on-site or in the purchaser’s vehicle.
Section B: Concrete Technology Important Notes
a. How will you determine the compressive strength of cement? Explain briefly the procedure.
Ans. Test for Compressive Strength of Cement: Testing material is cement, sand and water.
- 1. The required material for each cube is as follows:
- i. Cement – 200 gm,
- ii. Sand-600 gm,
- iii. Water quantity (P4 + 3) % of the total mass of cement and sand; where P is the standard consistency of cement.
- 2. The test specimens are 70.6 mm cubes having face area of about 5000 sq mm.
- 3. Large size specimen cubes cannot be made since cement shrinks and cracks may develop.
- 4. The temperature of water and test room should be 27° ± 2°C. A mixture of cement and standard sand in the proportion 1:3 by weight is mixed dry with a trowel for one minute and then with water until the mixture is of uniform colour.
- 5. Prepare three specimen cubes. Each cube’s substance is blended independently.
- 6. The total amount of cement, normal sand, and water is 185 g. 555 g and (P/4) + 3.5, where P is the percentage of water required to make a standard-consistency paste.
- 7. Place the mould on the vibration table after completely filling it with cement paste.
- 8. Vibrations are applied for approximately 2 minutes at a rate of 12000 ± 400 per minute.
- 9. The cubes are then removed from the moulds and immersed in clean fresh water before being tested in a compression testing equipment.
- 10. The compressive strength is calculated as the average of the three cubes’ results.
- 11. The load is applied at a rate of 35 N/sq mm/minute starting from zero.
- 12. The compressive strength is derived by multiplying the crushing load by the average area across which the load is delivered.
- 13. The result is expressed in N/mm2.
b. Write short notes on fly ash and GGBS.
Ans. A. Fly Ash: Fly ash is a type of debris produced by burning that consists of fine particles that rise with the flue gases. In the industrial setting, fly ash is typically defined as ash produced during the burning of coal.
Types of Fly Ash:
1. Class C Fly Ash:
- i. Because of its high Ca0 content, this type of fly ash is utilized as a solo stabilizing agent.
- ii. Adding lime improves the strength characteristics of class C fly ash with a CaO content of less than 25%.
2. Class F Fly Ash:
- i. This class of fly ash has a low CaO content.
- ii. Class F fly ash has an insufficient CaO content for the pozzolanic reaction to occur.
- iii. It is ineffective as a stabilizing agent on its own, but when combined with lime or lime and cement, it becomes an effective agent.
B. GGBS:
- 1. Blast furnace slag is a byproduct of the iron-making process. The furnace is fed with iron ore, coke and limestone, and the resulting molten slag floats above the molten iron at temperatures ranging from 1500°C to 1600°C.
- 2. The molten slag has a composition of about 30 % to 40 % SiO2, and about 40% CaO, which is close to the chemical composition of Portland cement.
c. Explain how will you determine the modulus of elasticity of concrete experimentally?
Ans. Test for Modulus of Elasticity: The test procedure involves two stages. Initially, the compressometer is set-up, followed by the application of load and testing.
A. Setting Up Compressometer: A compressometer is a device used to determine the strain and deformation properties of a concrete cylinder during compression testing. The following procedures are involved in the setup:
- 1. The compressometer is made up of two frames (top and bottom). The frames are initially constructed using spacers. During assembly, the spacers are maintained in place.
- 2. The pivot rod is held in place by screws that are then fastened into place. The tightening screws on the top and bottom frames are left free.
- 3. After arranging the compressometer, it is put on the concrete specimen on a level surface. The compressometer is positioned in the centre of the specimen.
- 4. After the location has been determined, the screws are tightened and the compressometer is secured to the specimen.
- 5. Once the setup is complete, unscrew and remove the spacers.
B. Testing the Specimen: The test procedure involves the following steps:
- 1.The compressometer-equipped specimen is put on the compression testing machine platform. It is appropriately centred.
- 2. The load application is performed continuously at a rate of 140 kg/cm2/minute without any obstruction.
- 3. The load application is continued until a stress value equal to (c +5) kg/cm2 is attained. Here c is the 1/3rd of average compressive strength of the cube. (The strength value of cube calculated to the nearest of 5 kg /cm2) which is a load of 12.4T.
- 4. Once this stress value is reached, it is maintained for a period of 60 seconds and then reduced to the stress of 1.5 kg/cm2 which is a load value of 0.37.
- 5. Again, the load is further increased until the stress of (c + 1.5) kg/cm2 is reached which is a load of 11.8T. At this point, compressometer reading is recorded.
- 6. Now, the load is gradually reduced and the readings are recorded at 17 intervals i.e., l1.87, 10.87, 9.87, 8.87, 7.87,……….1.8T, 0.37.
- 7. Repeat the test by applying the load for the third time and record the compressometer’s readings at an interval of 17 i.e., 11.8T, 10.8T, .8, 8.81, 7.81,………1.8T, 0.37 is determined.
C. Load-Deflection Graph:
- 1. From the observations, the load deflection graph is plotted for the loading conditions.
- 2. Tangents are drawn at the beginning of the graph and at the point of value equivalent to the concrete mix’s working stress. A line is drawn connecting the two spots.
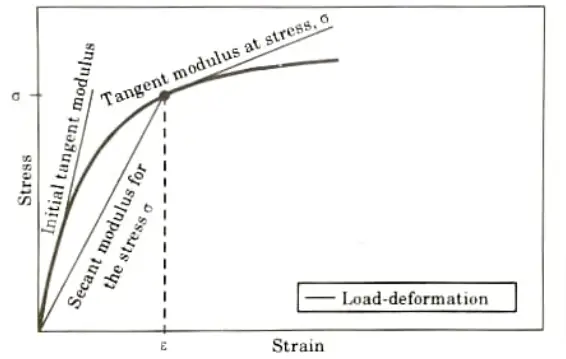
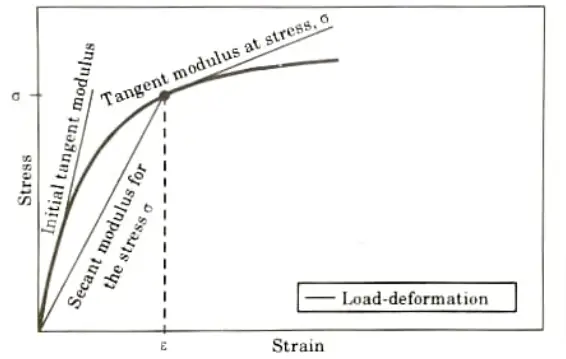
- 3. Slope of line joining initial tangent point and point of working stress gives:
Secant modulus = Stress/strain
d. What is the relation between compressive and tensile strength of concrete ?
Ans. Relation between Compressive and Tensile Strength of Concrete:
- 1. It is seen that concrete strength in compression and tension (both direct tension and flexural tension) are strongly related, but the relationship is not of the direct proportionality type.
- 2. The ratio of the two strengths is determined by the overall strength of the concrete.
- 3. In other words, higher compressive strength concrete has higher tensile strength, but the rate of tensile strength rise is decreasing.
- 4. The type of coarse aggregate has an impact on this relationship. Crushed aggregate has a higher flexural strength than a lower compressive strength.
- 5. This is due to the stronger bond between the cement paste and the aggregate particles.
- 6. Tensile strength of concrete is more vulnerable to poor curing than compressive strength.
- 7. This could be attributed to poor gel formation as a result of incorrect curing, as well as the fact that inadequately cured concrete may have more shrinkage fractures.
- 8. The addition of pozzolanic material to concrete increases its tensile strength.
- 9. From the extensive study, carried out at Central Road Research Laboratory (CRRD the following statistical relationship between tensile strength and compressive strength were established :
- i. Y = 15.3x – 9.00 for 20 mm maximum size aggregate.
- ii. y = 14.1x – 10.4 for 20 mm maximum size natural gravel.
- iii. y = 9.9x – 0.55 for 40 mm maximum size crushed aggregate.
- iv. y = 9.8x -2.52 for 40 mm maximum size natural gravel.
- where y is the compressive strength of concrete in MPa and x is the flexural strength of concrete in MPa.
- 10. Subjecting all the data to statistical treatment the following general relationship has been established at CRRI between flexural and compressive strength of concrete : y = 11x -3.4.
- 11. Flexural strength of concrete was determined to be 8 to 11 percent of compressive strength for higher concrete strength ranges (more than 25 MPa) and 9 to 12.8 percent for lower concrete strength ranges (less than 25 MPa).
- 12. The flexural to compressive strength ratio was higher in aggregates with a maximum size of 40 mm than in aggregates with a maximum size of 20 mm.
- 13. In general, the ratio of natural gravel to crushed stone was found to be slightly higher.
e. Discuss the properties of high weight concrete its applications.
Ans. A. Properties of High Weight Density Concrete: Following are the properties of high density concrete:
- 1. The strength of this concrete measured on standard cylinders has been found 42 MPa at 28 days for a water/cement ratio 0.58 and 24 MPa at water/cement ratio 0,9.
- 2. The density of this concrete for a mix of 1: 4.6: 6.4 with water/ cement ratio of 0.58 has been found as 3700 kg/m3.
- 3. The coefficient of thermal expansion of barite concrete measured in the range of temperature of 4 °C to 38 °C is found about twice that of normal concrete.
- 4. The modulus of elasticity and Poisson’s ratio of high density and normal concrete are nearly identical.
- 5. The shrinkage of high density concrete is approximately 1/4 to 1/3 that of standard concrete.
- 6. Thermal conductivity, diffusivity, and other properties of high strength concrete are significantly lower than those of conventional aggregate concrete.
- 7. Concrete constructed with barite aggregate does not weather well.
- 8. Since fine barite aggregate slows the setting and hardening process of concrete, trial mixes are recommended.
B. Applications of HDC: Following are the applications of HDC:
- 1 High density radiation shielding.
- 2. Precast blocks.
- 3. Mass concrete projects.
- 4. High density concrete applications columns.
- 5. Gravity seawall, coastal protection and breakwater structures.
- 6. Bridge counterweights.
- 7. Ballast for ocean vessels.
- 8. Off shore platforms noise and vibration dampening.
Section 3: Tests on Aggregate
a. Briefly describe the following tests on aggregate: specific gravity test, crushing test and impact test.
Ans. A. Crushing Test:
- 1. Aggregate crushing value is a relative measure of an aggregate’s resistance to crushing under gradually applied compressive load.
- 2. Aggregate is obtained after passing through a 12.5 mm sieve and remaining on a 10 mm sieve. Around 6.5 kg of surface dry aggregate was put in three levels in the standard cylinder, tamping each layer 25 times with a standard tamping rod. That has been levelled off. Its weight was discovered (A).
- 3 The plunger is put on the aggregate, taking care not to tilt it and jam the cylinder.
- 4. The assembly is then kept under compression testing machine for 10 minutes with a total load of 40 tonnes applied uniformly.
- 5. The load is released, the aggregate is removed, and it is sieved on a 2.36 mm sieve. The fraction of weight flowing through is (B).
- 6. Aggregate crushing value = B/A x 100% is the formula for calculating aggregate crushing value.
- 7. The aggregate crushing value should not exceed 45% for aggregate used for concrete other than wearing surfaces and 30% for concrete used for wearing surfaces such as runways, roadways, and so on.
B. Impact Test:
- 1. This test determines the relative resistance of aggregate to a sudden applied load or an impact load.
- 2. The test sample is aggregate that has passed through a 12.5 mm IS sieve and has been retained on a 10 mm IS sieve. The aggregate is oven dried for 4 hours at 110 °C.
- 3. The cup is filled with aggregate (weight A). By lifting the handle, the hammer is free to fall onto the aggregate in the cup as it is released by the tripping mechanism.
- 4. After 15 such blows, the aggregate is removed and sieved using a 2.36 mm sieve.
- 5. The fraction that passes through is weighted (weight B).
- 6. The fraction retained is also weighed (weight C). If (B + C) is less than A by more than 1 gram, the result is discarded and a fresh test is made.
- 7. The aggregate impact value is given by, Aggregate impact value = BA x 100.
C. Specific Gravity Test: Indian Standard Specification IS: 2386 (Part II) of 1963 gives various procedures to find out the specific gravity of different sizes of aggregates. The following procedure is applicable to aggregate size larger than 10 mm.
- 1. A sample of aggregate weighing at least 2 kg is obtained. It is extensively cleaned to eliminate any finer particles or dust that may have adhered to the aggregate.
- 2. It is then placed in a wire basket and soaked in distilled water at a temperature ranging from 22 to 32 degrees Celsius.
- 3. Shortly following immersion, the entrapped air in the sample is evacuated by lifting the basket containing it 25 mm above the tank’s base and letting it to drop 25 times at a rate of around one drop per second.
- 4. During the operation, care is taken that the basket and aggregate remain completely immersed in water. They are kept in water for a period of 24 ± 1/2 hours afterwards.
- 5. The basket and aggregate are then jolted and weighed (weight A1) in water at a temperature 22° to 32 °C.
- 6. The basket and the aggregate are then removed from water and allowed to drain for a few minutes and then the aggregate is taken out from the basket and placed on dry cloth and the surface is gently dried with the cloth.
- 7. The aggregate is transferred to the second dry cloth and further dried.
- 8. The empty basket is again immersed in water, jolted 25 times and weighed in water (weight A2).
- 9. The aggregate is exposed to atmosphere away from direct sunlight for not less than 10 minutes until it appears completely surface dry.
- 10. Then the aggregate is weighed in air (weight B). Then the aggregate is kept in the oven at a temperature of 100 to 110 °C and maintained at this temperature for 24 ± 12 hours.
- 11. It is then cooled in the air-tight container, and weighed (weight C).
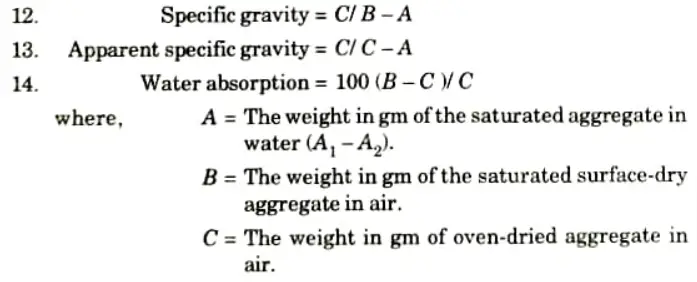
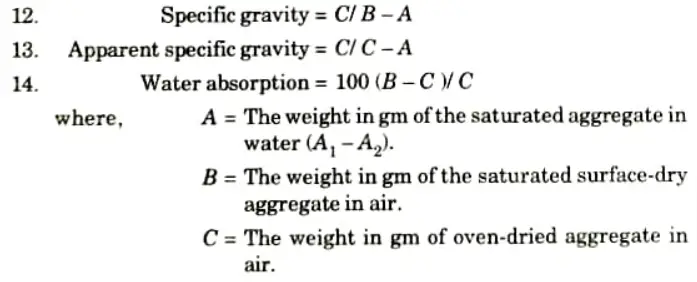
b. Explain with chemical reaction hydration of high alumina cement.
Ans. Hydration of High Alumina Cement:
- 1. The approximate chemical oxide composition is as follows:
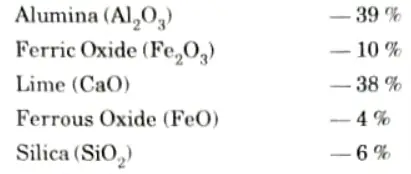
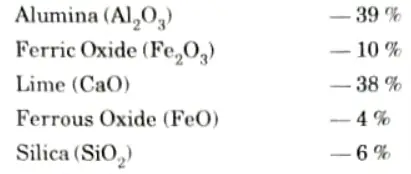
- 2. During hydration of HAC initially monocalcium aluminate decahydrate (CAH10), dicalcium aluminate octahydrate (C2AH8) and alumina get (AH3) are formed.
- 3. However, these compounds of hydration are metastable and at normal temperature convert gradually to a more stable tricalcium aluminate hexahydrate (C3AH6).
- 4. This conversion is accompanied by a loss of strength and a change in crystal form from hexagonal to cubical, resulting in the release of water, a reduction in solids volume, and an increase in porosity. 6%
- 5. Increased porosity makes it more vulnerable to chemical attack. The rate of conversion increases as the temperature rises.
- 6. The hydration and conversion processes can be symbolically represented as:


Section 4: Concrete Properties
a. Describe the effect of following admixtures on cement concrete and give three examples of each. Retarders, accelerators and water proofers.
Ans. A. Effects of Retarders:
- 1. Retarders often increase the setting time and hence delay cement setting.
- 2. Because these slow the rate of hydration, more water is accessible and the workability improves.
- 3. Retarders boost compressive strength during freezing and thawing.
- 4. A 0.2 percent sugar by mass addition slows the hydration of cement to the point that the final set may not occur even after 72 hours.
- 5. It has also been discovered that adding 0.1% sugar by mass of cement boosts the strength of the cement after 3 days and increases the strength after 28 days by 30%.
- 6. Retarders are critical in instances when grouting is required for voids behind concrete arches, tunnel lining, and so on.
- 7. They also improve the link between subsequent lifts in concrete structures.
- 8. Example: Calcium sulphate, sugar, starch, cellulose, amnonium, ferrous and ferric chlorides, sodium lignosulphonic hexametaphosphate, acid and their salts, carbohydrates, hydro carboxylic acids and their salts are a few examples of retarders.
B. Effects of accelerators:
- 1. The general action of accelerators is to produce faster breakdown of cement compounds, notably tricalcium silicate, in water, allowing for faster hydration of these compounds.
- 2. Using 2% calcium chloride by mass of cement can minimise setting ume by one-third while increasing one to seven day compressive strength by 3 to 8 MPa.
- 3. Flexural strength increased by 40 to 80% in one day and up to 12% in 28 days.
- 4. Large doses of CaCl2 result in flash set of concrete and the ambient temperature.
- 5. Calcium formate (a fine powder), which is somewhat less soluble than calcium chloride and is less effective does not have the same adverse effect on corrosion of embedded steel as CaCl2. It is added in the same dosages.
Examples: Calcium chloride, sodium nitrate, calcium nitrate, etc.
C. Effects of Water Proofers:
- 1. Water proofers cement mortar or concrete should be impenetrable to water under pressure and have a high resistance to water absorption.
- 2. Water repellent additives or pore filler additives can be used to make concrete water resistant. Yet, the ultimate goal is to create water-resistant concrete.
- 3. Chemically active water repellent compounds include soda and potash soaps, whereas chemically inactive materials include calcium soaps, resin, vegetable oil, fats, waxes and coal tar residue.
- 4. Pore filling materials include alkaline silicates, particularly soda silicate, aluminium and zinc sulphate, and aluminium and calcium chlorides.
b. Explain the effect of concrete properties while adding silica fumes and GGBS.
Ans. Effect of Silica Flume:
- 1. Drying Shrinkage: The inclusion of silica fume has no effect on the long-term shrinkage of concrete.
- 2. Creep: The creep of silica fume-containing concrete will be less than that of equivalent Portland cement concrete.
- 3. Chemical Resistance: The reduction in the CalOH), content of the cement paste, which decreases linearly with the amount of silica fume added, is a primary cause for the enhanced resistance of concrete to acidic and sulphate waters.
- 4. Alkali Aggregate Reaction: In comparison to fly ash, which requires 30% – 40% replacement, less than 10% silica fume is shown to be adequate for minimizing alkali aggregate expansion.
- 5. Strength: Strength of 62-80 MPa can be easily achieved.
- 6. Permeability: With a 10% addition of silica fume by weight of cement, silica fume reduces the number of voids in hydrated cement paste, making it practically impermeable even at early ages.
- 7. Freeze and thaw Effect: The effect of silica fume concrete on freeze thaw affect is not very significant.
Effects of GGBS:
- 1. Decrease strength and rate of strength gain.
- 2. Increase the resistance to freezing and thawing.
- 3. Increase the resistance to deicing chemicals.
- 4. Increase the resistance to the corrosion of reinforcement.
- 5. Reduction of expansion due to alkali-silica reaction (ASR).
- 6. Increase the resistance to sulfate attack.
- 7. Reduce the permeability.
Section 5: Methods of Mix Design
a. Discuss briefly the effects of adding mineral admixtures to cement concrete.
Ans. A. Effect of Fly Ash:
- 1. On Amount of Mixing Water:
- i. Because of the fineness of the fly ash, the use of fly ash in restricted amounts as a replacement for cement or as an additive to cement requires a bit more water for the same slump.
- ii. It is generally agreed that the use of fly ash, particularly as an additive rather than a replacement for cement, lowers segregation and bleeding.
- iii. Adding fly ash to coarse sand gives good outcomes; adding it to fine sand may increase the water need for a given workability.
- 2. On Compressive Strength: An addition of up to 30% fly ash may result in lesser strength at 7 and 28 days, but may be nearly equal at 3 months and may grow further at ages more than 3 months if curing is maintained.
- 3. On Modulus of Elasticity: It is lower at early ages and higher at later ages.
- 4. On Curing Condition: It is similar to Portland cement concrete.
- 5. On Shrinkage of Concrete: Coarse fly ash and fly ash with a high carbon concentration are more likely to induce drying shrinkage than finer fly ash and fly ash with a low carbon content.
- 6. On Permeability: The permeability of concrete reduces on addition of fly ash to cement.
- 7. On Resistance to Chemical Attack: Fly ash slightly improves the resistance of concrete to sulphate attack.
- 8. On Heat of Hydration: In concrete, fly ash decreases the heat of hydration. A 30% fly ash substitute may result in a heat of hydration reduction of 50-60%.
- 9. On Air Entrainment: The presence of fly ash reduces the amount of air entraining agent.
- 10. On Setting Time: A 30 % substitution of fly ash may result in an increase of initial setting time up to 2 hours.
B. Effect of Silica Flume:
- 1. Drying Shrinkage: Long term shrinkage of concrete is not affected significantly by the addition of silica fume.
- 2. Creep: The creep of concrete containing silica fume will be lower than corresponding Portland cement concrete.
- 3. Chemical Resistance: The reduction in the CalOH), content of the cement paste, which decreases linearly with the amount of silica fume added, is a primary cause for the enhanced resistance of concrete to acidic and sulphate waters.
- 4. Alkali Aggregate Reaction: Less than 10 % of silica fume is found adequate for reducing the alkali aggregate expansion as compared to fly ash which requires 30% – 40% replacement.
- 5. Strength: Strength of 62-80 MPa can be easily achieved.
- 6. Permeability: With a 10% addition of silica fume by weight of cement, silica fume reduces the number of voids in hydrated cement paste, making it practically impermeable even at early ages.
- 7. Freeze and thaw Effect: The effect of silica fume concrete on freeze thaw affect is not very significant.
C. Effects of GGBS:
Effects of GGBS on the Properties of Fresh Concrete:
- 1. Due to the higher paste content and paste’s increased cohesiveness, the cementitious material containing GGBS displayed greater workability.
- 2. When GGBS is used in concrete mixtures to replace some of the Portland cement, an increase in setting time is typically to be expected.
- 3. When GGBS is substituted for Portland cement on an identical mass basis, bleeding is decreased because GGBS is finer.
- 4. The pace and volume of bleeding may increase as the GGBS becomes more coarse.
Effects of GGBS on the Properties of Hardened Concrete:
- 1. Decrease strength and rate of strength gain.
- 2. Increase the resistance to freezing and thawing.
- 3. Increase the resistance to deicing chemicals.
- 4. Increase the resistance to the corrosion of reinforcement.
- 5. Reduction of expansion due to alkali-silica reaction (ASR).
- 6. Increase the resistance to sulfate attack.
- 7. Reduce the permeability.
D. Effects of Metakaolin:
- 1. In HSC, an additive called metakaolin replaces some of the cement (high strength concrete).
- 2. If a concrete’s compressive strength is greater than 40 MPa, it is referred to as high strength concrete.
- 3. Kaolin (a clay mineral) is calcined at a temperature between 650 and 8000C to create metakaolin. It possesses pozzolanic qualities.
- 4. Chemical formula of Metakaolin is Al2O3.2SiO2.2H2O
- 5. It reacts with Ca(OH)2 one of the by-products of hydration reaction of cement and results in additional C-S-H gel which results in increased strength.
E. Effect of Rice Husk Ash on Concrete:
- 1. Rice husk ash gives strength to the concrete.
- 2. Because its particle size is significantly smaller than that of cement, it also reduces permeability.
- 3. It lowers the temperature at which concrete hydrates.
- 4. Rice husk ash increases the concrete’s resilience to attacks from chloride and sulphate.
b. List the various methods of mix design. Briefly describe the IS method.
Ans. Methods of Mix Design: Following are the various methods of proportioning concrete mixes:
- i. Trial mixes.
- ii. Nominal mixes.
- iii. America concrete institute method.
- iv. BIS method.
- v. Minimum voids method.
- vi. Maximum density method.
IS Method:
Step 1: Calculation of Target Strength of Concrete:
Target strength is denoted by ft which is obtained by characteristic compressive strength of concrete at 28 days (fck) and value of standard deviation (𝛔)


Standard deviation can be taken from below table.
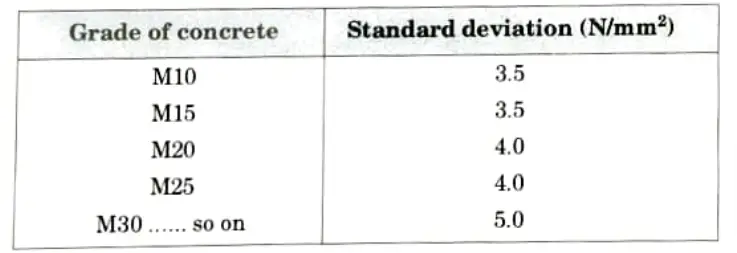
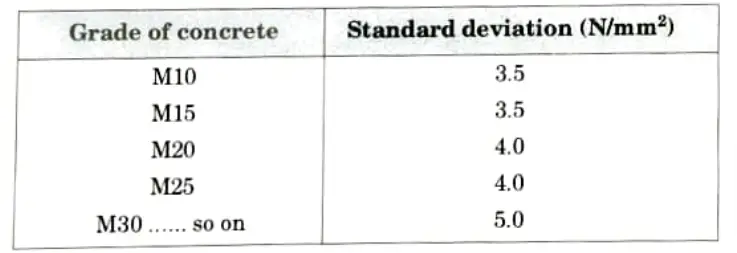
Step 2: Selection of Water-Cement Ratio:
Water cement ratio is selected from the below curve for 28 days characteristic compressive strength of concrete.
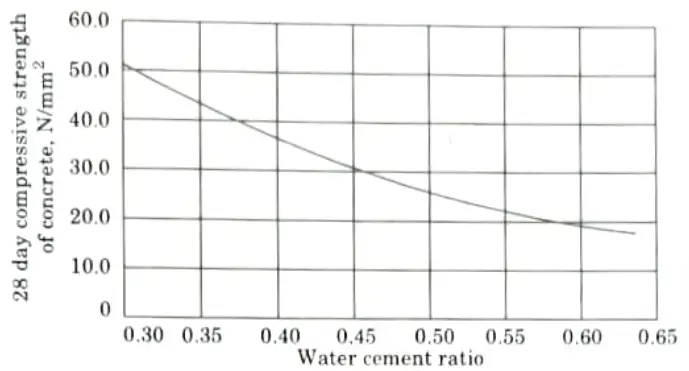
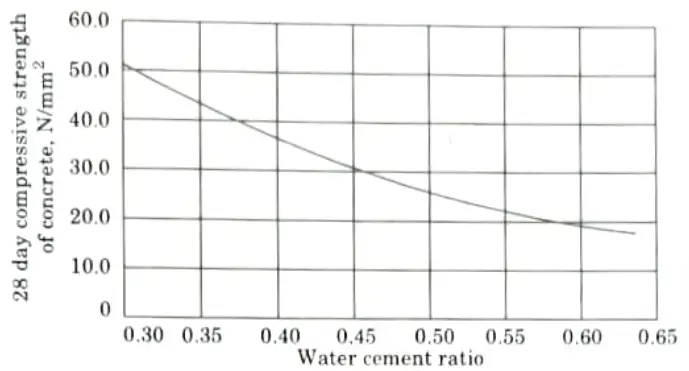
Step 3: Determination of Aggregate Air Content:
i Air content in the concrete mix is determined by the nominal maximum size of aggregate used.
ii. Below table will give the entrapped air content in percentage of volume of concrete.
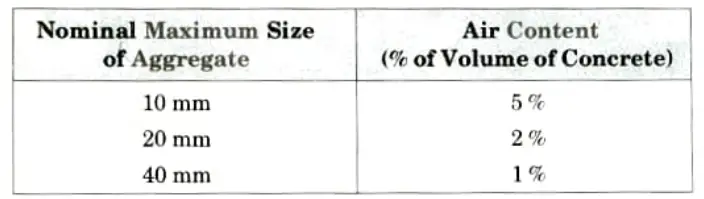
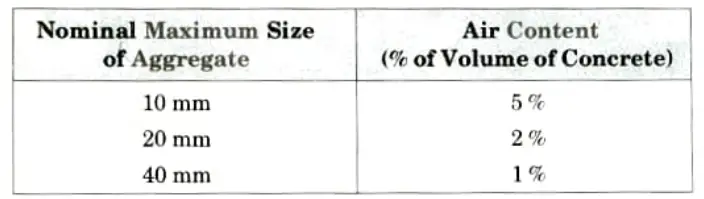
Step 4: Selection of Water Content for Concrete:
i. Using the nominal maximum size of the aggregate listed in the table below, choose the water content that will assist you achieve the required workability.
ii. When only angular-shaped aggregates are used in concrete and the slump ranges between 25 and 50 mm, the table below is employed.
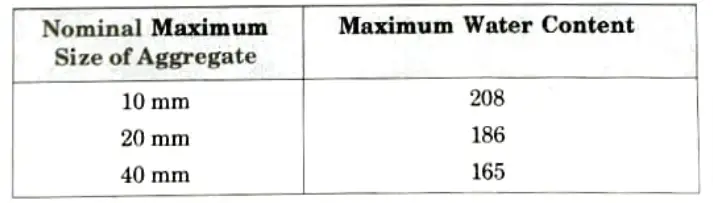
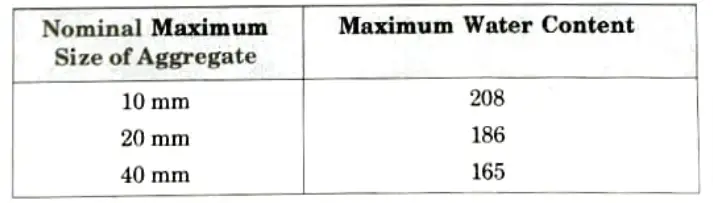
Step 5: Selection of Cement Content for Concrete: Step 2 determines the water-cement ratio, and Step 4 determines the water amount. With these two conditions, we can readily calculate the amount of cement. Nonetheless, the value should meet the minimal requirements listed in the table. The amount of cement content is determined by which of the two quantities is larger.
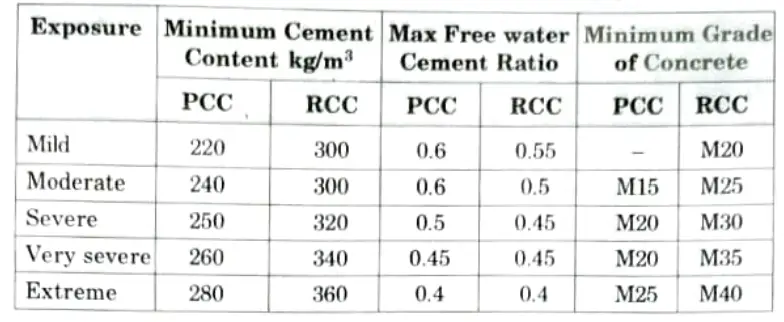
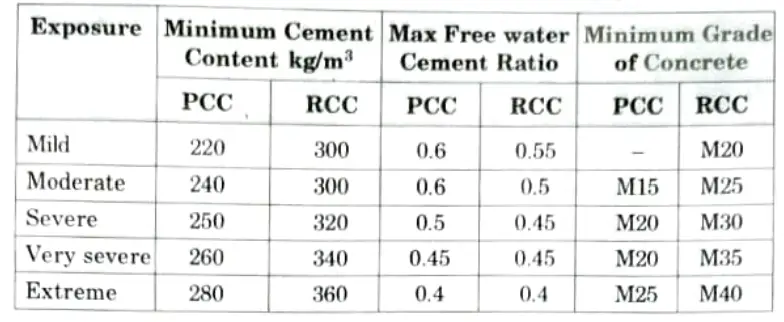
Step 6: Calculation of Aggregate Ratio: Using the table below, we can determine the volume ratio of coarse aggregate to total aggregate for various zones of fine aggregates for the specified nominal maximum aggregate size.
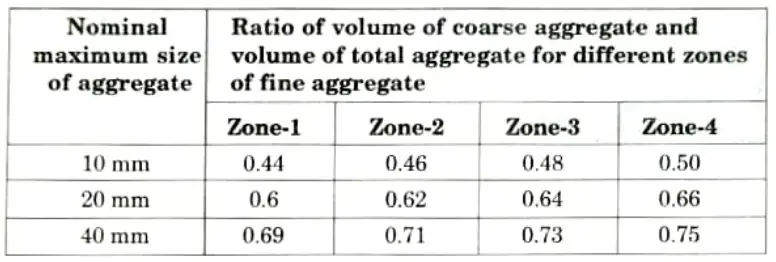
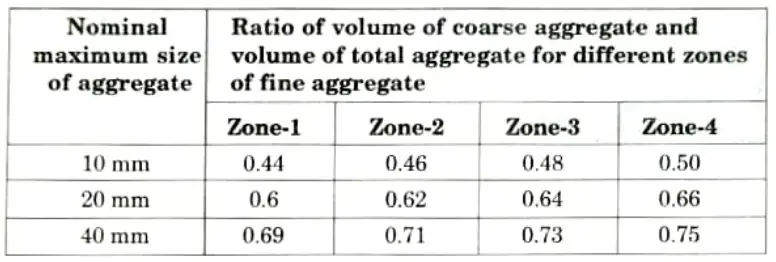
Step 7: Calculation of Aggregate Content for Concrete: The ratio of coarse to fine aggregate volume has previously been calculated. So, it is extremely simple to calculate the volume of fine aggregate from one volume of coarse aggregate.
Mass of fine aggregate is calculated from below formula
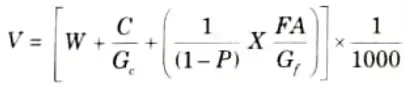
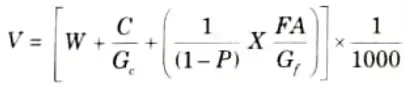
Similarly, mass of coarse aggregate is calculated from below formula.
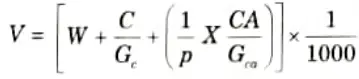
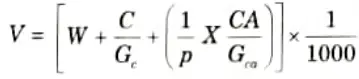
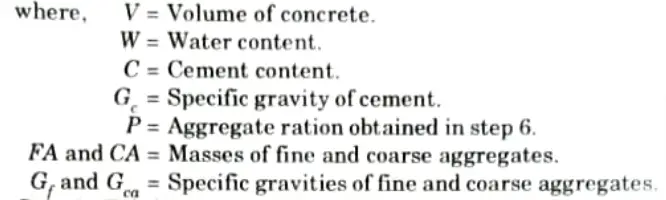
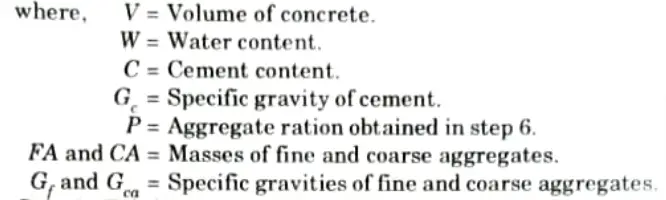
Step 8 : Trial Mixes for Testing Concrete Mix Design Strength: Make at least three cubes of 150 mm in size in accordance with the aforementioned specifications and conduct a trail test based on the values acquired above. Check the cubes to see if the necessary strength was obtained. If not, rethink the mixture and make the necessary adjustments until the cube reaches the requisite strength.
Section 6: Mix Proportioning
a. Design a concrete mix for construction of an elevated water tank. The specified strength of concrete is 30 MPa at 28 days measured on standard cylinders. Standard deviation can be taken as 4 MPa. The specific gravity of FA and CA are 2.65 and 2.7 respectively. The dry rodded bulk density of CA is 1600 kg/m3 and fineness modulus of FA is 2.80. Ordinary Portland cement (type 1) will be used. A slump of 50 mm is necessary. CA is found to be absorptive to the extent of 1% and free surface moisture in sand is found to be 2 %. Assume any other essential data by ACI committee method.
Ans. 1. Assuming 5 percent of results are allowed to fall below specified design strength. The mean strength,


2. Since OPC is used, from ACI 211.1 1991, the estimated w/e ratio is 0.47.
i. This w/c ratio from strength point of view is to be checked against maximum w/c ratio given for special exposure condition given in ACI 211.1: 1991 and minimum of the two is to be adopted.
ii. From exposure condition ACI 211.1: 1991 the maximum w/e ratio is 0.50
Therefore, adopt w/c ratio of 0.47.
3. From ACI 211.1: 1991, for a slump of 50 mm, 20 mm maximum size of aggregate, for non-air-entrained concrete, the mixing water content is 185 kg/m3 of concrete. Also the approximate entrapped air content is 2 %.


4. From ACI 211.1: 1991, for 20 mm coarse aggregate, for fineness modulus of 2.80, the dry rodded bulk volume of coarse aggregate is 0.62 per unit volume of concrete.
5. Therefore the weight of coarse aggregate = 0.62 x 1600 = 992 kg/m3.
6. From ACI 211.1: 1991, the first estimate of density of fresh concrete for 20 mm maximum size of aggregate and for non-air-entrained concrete = 2355 kg/m3.
7. The weight of all the known ingredient of concrete


8. Alternatively the weight of FA can also be found out by absolute volume method which is more accurate, as follows:
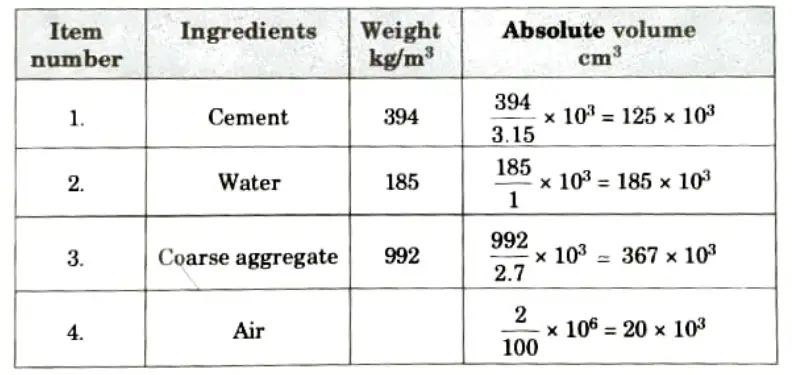
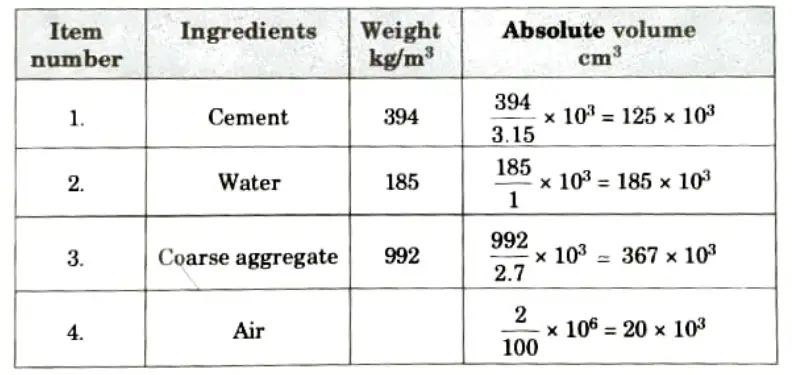


9. Estimated quantities of materials per cubic meter of concrete are:
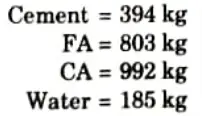
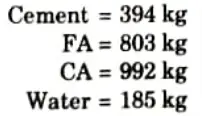
Density of fresh concrete 2374 kg/m3 as against 2355 read from ACI 211.1:1991.
10. Proportions:


Weight of materials for one bag mix in kg = 50 : 102 : 126 : 23.5
The above quantity is on the basis that both FA and CA are in saturated and surface dry condition.
11. The proportions are required to be adjusted for the field conditions. FA has moisture of 2 per cent.
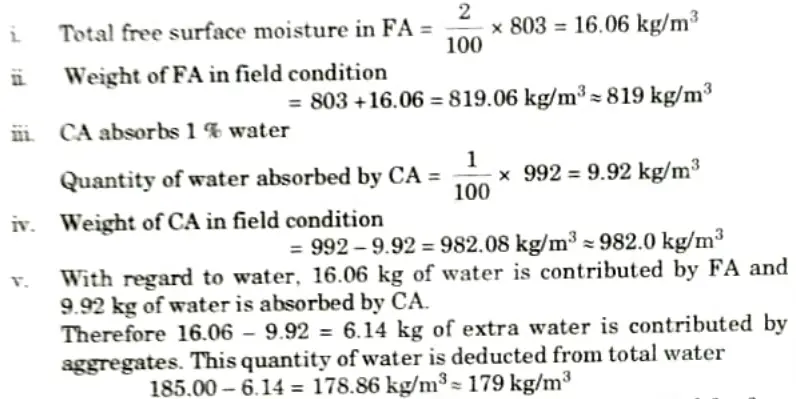
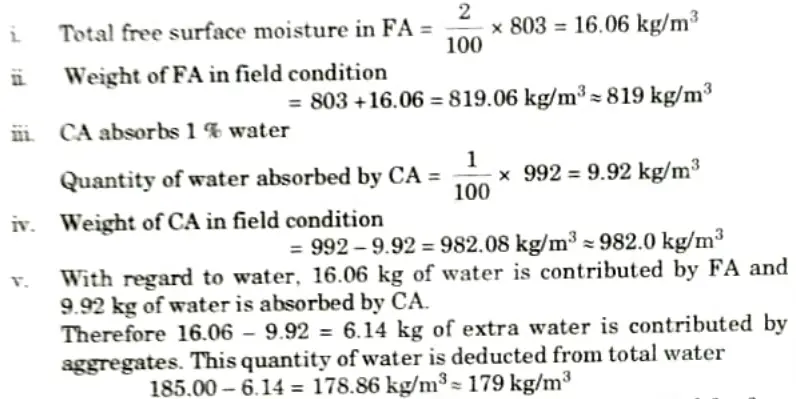
12. Quantities of materials to be used in the field duly corrected for free surface moisture in FA and absorption characteristic of CA
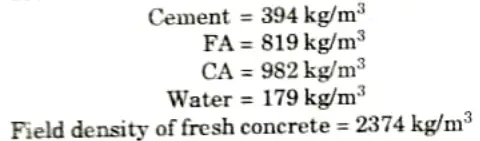
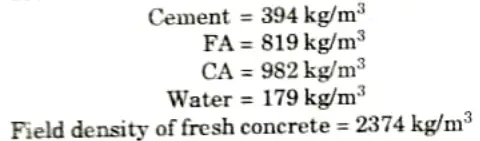
b. What data required for mix proportioning ? Describe with point to point.
Ans. Required Data: Following are the data required for mix proportioning:
- i. Grade of concrete.
- ii. Maximum size of aggregate.
- iii. Minimum cement content.
- iv. Maximum w/c ratio.
- v. Workability in term of slump.
- vi. Exposure conditions.
- vii. Maximum temperature at the pouring point.
- viii. Early age strength (if required).
- ix. Grading zone of the aggregate.
- x. Type of aggregate.
- xi. Maximum cement content.
- xii. What kind of admixture is used – Brand name.
- xiii. Specific gravity of all the materials used and dosage etc.
Section 7: Self Compacting Concrete
a. Explain the mineral admixtures for self compacting concrete.
Ans. A. Self Compacting Concrete:
- 1. Self-compacting or self-consolidated concrete is a highly flowable, non-segregating concrete that fills the formwork without the use of any vibrators and spreads into crowded reinforcement areas.
- 2. Self-compacting concrete offers more freedom, denser reinforcement, and optimum concrete sections and shapes.
- 3. It benefits from retaining durability and features and benefits from satisfying performance expectations.
- 4. It has been employed best in areas with a high concentration of pipelines and rebars, columns, drilled shafts, and bridges.
- 5. The self-compacting concrete enhances constructability, lowers skilled labour costs and noise levels, decreases voids in heavily reinforced areas, provides improved strength and durability, and provides a clean and uniform surface finishing. It also speeds up project timelines.
- 6. Several mineral admixtures, such as fly ash, silica fume, ground-granulated blast-furnace slag, and limestone powder, are utilized in SCC.
B. Mineral Admixtures:
- 1. Fly Ash: Fly ash in appropriate quantity may be added to the improve quality and durability of SCC.
- 2. Ground Granulated Blast Furnace Slag (GGBS): To enhance the rheological qualities, GGBS, a substance that is both cementitious and pozzolanic, may be added.
- 3. Silica Fume: Silica fume may be added to improve the mechanical properties of SCC.
- 4. Stone may be Powder: Finely crushed lime stone, dolomite or granite added to increase the powder content. The fraction should be less than 125 micron.
- 5. Fibres: Fibres may be used to enhance the properties of SCC in the same way as tor normal concrete.
b. Explain comparison between traditional and SSC constituents with neat sketch.
Ans. Super-sulphated Cement (IS 6909-1990):
- 1. To make super-sulphated cement, a mixture of 80–85 percent granulated slag, 10–15 percent hard burned gypsum, and around 5 percent Portland cement clinker is ground together.
- 2. The merchandise is pulverised more finely than Portland cement. Per gramme, the specific surface cannot be less than 4000 cm2.
- 3. Compared to Portland cement, this cement is somewhat more susceptible to deterioration during storage.
- 4. The low heat of hydration of super-eulphated cement is 40–45 calories/gm at 7 days and 45–50 at 28 days.
- 5. This cement is highly resistant to sulphates. This cement is especially suggested for use in foundations where chemically hostile circumstances occur because of its feature.
- 6. Super-sulphated cement is also utilised in maritime works because it is more resistant to attack by sea water than Portland blast furnace slag cement.
- 7. Construction of reinforced concrete pipes that will likely be buried in sulphate-bearing soils is another application for super-sulphated cement.
- 8. Improved resistance to sulphate attack is the result of the substitution of granulated slag.
- 9. In comparison to Portland cements, super-sulphated cements, particularly high alumina cement, mix with more water during hydration.
- 10. After casting, wet curing must continue for at least three days since hasty drying produces an unattractive or powdery top layer.
- 11. The water to cement ratio when using super-sulphated cement should not be less than 0.5, and a mix leaner than approximately 1:6 is also not advised.
6 thoughts on “Concrete Technology: Aktu Question Paper with Answers, Notes”